Surface thermal treatment process for metal workpiece
A technology for surface heat treatment and metal parts, which is used in heat treatment equipment, manufacturing tools, quenching agents, etc., can solve the problems of unpredictable heat treatment effect, large deformation of metal workpieces, affecting service life, etc., saving energy consumption and improving resistance. Tensile strength, anti-shedding effect
- Summary
- Abstract
- Description
- Claims
- Application Information
AI Technical Summary
Problems solved by technology
Method used
Examples
Embodiment 1
[0021] A heat treatment process for the surface of metal parts, said process comprising the following steps:
[0022] Step 1: Metal parts are pickled in hydrochloric acid solution, ultrasonic treatment is carried out in the later stage of treatment, and finally rinsed with pure water in sequence
[0023] Wash, dry and set aside;
[0024] Step 2: Heat the heating furnace to 1550°C, put the metal plates to be heat-treated into the heating furnace and burn them for later use;
[0025] Step 3: Soak the heat-treated metal plate in an aqueous solution for 12 minutes to realize heat treatment and rust removal on the metal surface;
[0026] Step 4: Put the metal parts into the vacuum heating machine and heat them by laser flame spraying, heating to a temperature of 1020°C, and continue heating for 15 minutes;
[0027] Step 5: Then transfer the normalized metal parts to the salt bath furnace until the temperature of the metal parts drops to 600 ° C, and then transfer the metal parts ...
Embodiment 2
[0035] A heat treatment process for the surface of metal parts, said process comprising the following steps:
[0036] Step 1: The metal parts are pickled in hydrochloric acid solution, ultrasonic treatment is performed in the later stage of treatment, and finally rinsed with pure water, dried, and set aside;
[0037] Step 2: Heat the heating furnace to 1700°C, put the metal plates to be heat-treated into the heating furnace and burn them for later use;
[0038] Step 3: Soak the heat-treated metal plate in an aqueous solution for 14 minutes to realize heat treatment and rust removal on the metal surface;
[0039] Step 4: Put the metal parts into the vacuum heating machine and heat them by laser flame spraying, heating to a temperature of 1020°C, and continue heating for 15 minutes;
[0040] Step 5: Then transfer the normalized metal parts to the salt bath furnace until the temperature of the metal parts drops to 625°C, and then transfer the metal parts to the air furnace for h...
Embodiment 3
[0048] A heat treatment process for the surface of metal parts, said process comprising the following steps:
[0049] Step 1: The metal parts are pickled in hydrochloric acid solution, ultrasonic treatment is performed in the later stage of treatment, and finally rinsed with pure water, dried, and set aside;
[0050] Step 2: Heat the heating furnace to 1850°C, put the metal plates to be heat-treated into the heating furnace and burn them for later use;
[0051] Step 3: Soak the heat-treated metal plate in an aqueous solution for 15 minutes to realize heat treatment and rust removal on the metal surface;
[0052] Step 4: Put the metal parts into the vacuum heating machine and heat them by laser flame spraying, heating to a temperature of 1020°C, and continue heating for 15 minutes;
[0053] Step 5: Then transfer the normalized metal parts to the salt bath furnace until the temperature of the metal parts drops to 650 ° C, and then transfer the metal parts to the air furnace for...
PUM
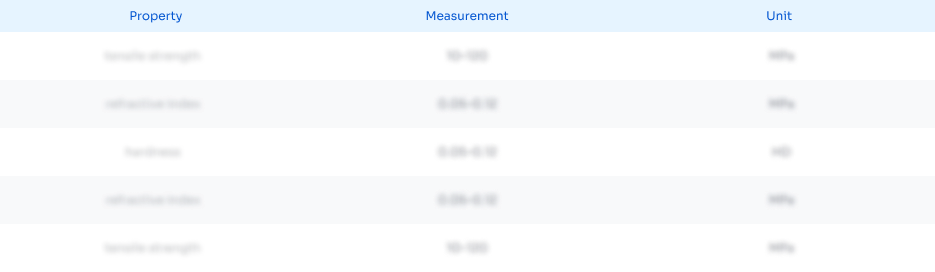
Abstract
Description
Claims
Application Information

- Generate Ideas
- Intellectual Property
- Life Sciences
- Materials
- Tech Scout
- Unparalleled Data Quality
- Higher Quality Content
- 60% Fewer Hallucinations
Browse by: Latest US Patents, China's latest patents, Technical Efficacy Thesaurus, Application Domain, Technology Topic, Popular Technical Reports.
© 2025 PatSnap. All rights reserved.Legal|Privacy policy|Modern Slavery Act Transparency Statement|Sitemap|About US| Contact US: help@patsnap.com