Depth sensor calibration system and method
A depth sensor and calibration system technology, applied in the field of depth sensors, can solve the problems of test environment, signal strength test accuracy limitation, etc., and achieve the effect of improving performance and calibration accuracy
- Summary
- Abstract
- Description
- Claims
- Application Information
AI Technical Summary
Problems solved by technology
Method used
Image
Examples
Embodiment Construction
[0042] In order to better understand the above technical solutions, the technical solutions of the embodiments of this specification will be described in detail below through the drawings and specific examples. It should be understood that the embodiments of this specification and the specific features in the embodiments are the technical solutions of the embodiments of this specification. It is a detailed description, rather than a limitation to the technical solutions of this specification. In the case of no conflict, the embodiments of this specification and the technical features in the embodiments can be combined with each other.
[0043] An embodiment of the present invention provides a depth sensor calibration system, such as figure 1 As shown, it includes a calibration processing module 101 , a delay processing module 102 , a depth sensor 103 and a transmitting module 104 .
[0044] Optionally, a power module 105 is also included.
[0045] The depth sensor calibration...
PUM
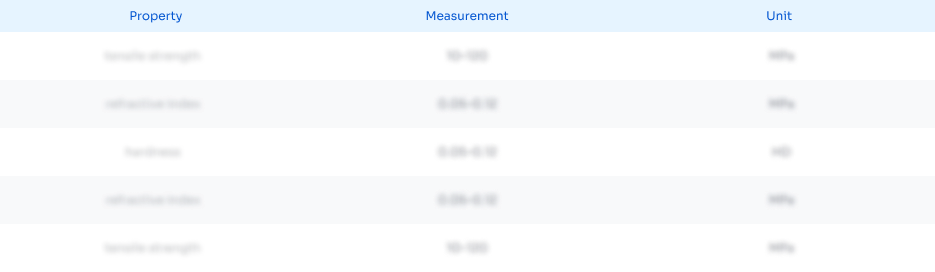
Abstract
Description
Claims
Application Information

- Generate Ideas
- Intellectual Property
- Life Sciences
- Materials
- Tech Scout
- Unparalleled Data Quality
- Higher Quality Content
- 60% Fewer Hallucinations
Browse by: Latest US Patents, China's latest patents, Technical Efficacy Thesaurus, Application Domain, Technology Topic, Popular Technical Reports.
© 2025 PatSnap. All rights reserved.Legal|Privacy policy|Modern Slavery Act Transparency Statement|Sitemap|About US| Contact US: help@patsnap.com