Method for testing output characteristics of stacked piezoelectric ceramics under large-range temperature change
A technology of piezoelectric ceramics and output characteristics, applied in the field of active vibration control of wind tunnel models, can solve the problems that engineering and test systems cannot be applied, and the displacement difference between the piezoelectric ceramics under test and the displacement sensor is not considered, and the experimental test method is achieved. Accurate, avoid damage, high temperature control effect
- Summary
- Abstract
- Description
- Claims
- Application Information
AI Technical Summary
Problems solved by technology
Method used
Image
Examples
Embodiment Construction
[0029] specific implementation plan
[0030] The specific implementation method of the present invention will be described in detail below in conjunction with the technical scheme and accompanying drawings.
[0031] Such as figure 2 As shown, a comprehensive test system based on the output performance of the stacked piezoelectric ceramic actuator consists of a base 5, an optical fiber displacement sensor 1, a U-shaped plate 2, a spacer 3, and a stacked piezoelectric ceramic actuator 4. It consists of a pressure sensor 6, a T-shaped base 10, a test system 7, a computer 8 and a high and low temperature environment box 9.
[0032] figure 1 It is the schematic diagram of the comprehensive experimental system of the present invention. Firstly, the preset preload force of the test is given to the stacked piezoelectric ceramic actuator. The real-time preload value can be obtained by the pressure sensor, which is pasted on the stacked piezoelectric ceramic actuator. The strain gau...
PUM
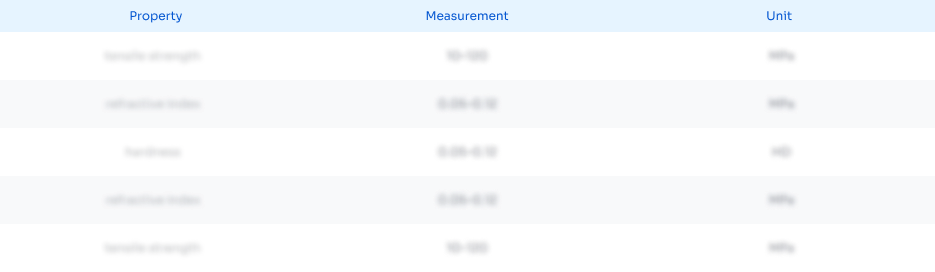
Abstract
Description
Claims
Application Information

- Generate Ideas
- Intellectual Property
- Life Sciences
- Materials
- Tech Scout
- Unparalleled Data Quality
- Higher Quality Content
- 60% Fewer Hallucinations
Browse by: Latest US Patents, China's latest patents, Technical Efficacy Thesaurus, Application Domain, Technology Topic, Popular Technical Reports.
© 2025 PatSnap. All rights reserved.Legal|Privacy policy|Modern Slavery Act Transparency Statement|Sitemap|About US| Contact US: help@patsnap.com