A kind of cutting edge cutting edge processing method
A processing method and cutting edge cutting technology, applied in the field of cutting edge cutting edge surface processing, can solve the problems of low production efficiency, poor processing precision of cutting edge cutting edge surface, etc. The effect of speed increase
- Summary
- Abstract
- Description
- Claims
- Application Information
AI Technical Summary
Problems solved by technology
Method used
Image
Examples
Embodiment 1
[0092] A method for processing the edge surface of a broken edge shearing edge, the steps are as follows:
[0093] 1. Turning: install the cutting edge to be processed on the turning and grinding fixture and then assemble it into the lathe, and the lathe will perform rough turning on the surface 103 of the cutting edge cutting edge to be processed;
[0094] 2. Milling: Install the broken edge cutting edge after rough turning in step 1 on the milling fixture and then assemble it into the milling machine, and the milling machine will perform milling processing on the broken edge cutting edge surface 103;
[0095] 3. Grinding: Install the broken edge shearing blade after milling in step 2 on the turning-grinding fixture and then assemble it into the grinding machine, and the grinding machine performs fine grinding processing on the broken edge shearing edge surface 103 .
[0096] like Figure 20 As shown in the figure, the cutting edge cutting edge processing method of the prese...
Embodiment 2
[0099] like figure 1 and Image 6 As shown, a method for processing the edge surface of a broken edge shearing edge in the present embodiment is further improved on the basis of Embodiment 1, and the turning and grinding fixture includes:
[0100] The base body 11, which is a columnar body;
[0101] an assembling table 110, which is arranged at the center of one end face of the base body 11, and is used for assembling the fixture on the machine tool;
[0102] The mounting surface 12 is a plane disposed on the side surface of the base body 11, and the mounting surface 12 is horizontal with the central axis of the base body 11;
[0103] a mounting hole 120, which is formed on the mounting surface 12, and whose shape matches the mounting hole 102 of the cutting edge shear;
[0104] The concave structure 13 is formed on one side of the mounting surface 12 along the central axis of the base body 11 , and is used for placing the lower eaves 101 of the broken edge cutting edge.
...
Embodiment 3
[0112] like figure 1 , figure 2 , image 3 , Figure 4 and Figure 11 As shown, a method for processing the edge surface of a broken edge shearing edge in this embodiment is further improved on the basis of Embodiment 2. The concave structure 13 of the turning and grinding fixture includes:
[0113] A concave step 130, which is arranged along the central axis of the base body 11, is in the shape of a concave second-level step, and is opened on one side of the mounting surface 12;
[0114] a fastening plate 131, which is detachably connected to the secondary vertical surface 1302 of the concave step 130;
[0115] The fastening plate 131 and the first-level lateral surface 1300 and the first-level vertical surface 1301 of the concave step 130 form a groove structure.
[0116] The concave structure 13 can be a variety of structures, such as a groove directly opened on one side of the mounting surface 12, but the directly opened groove structure has certain defects, and the ...
PUM
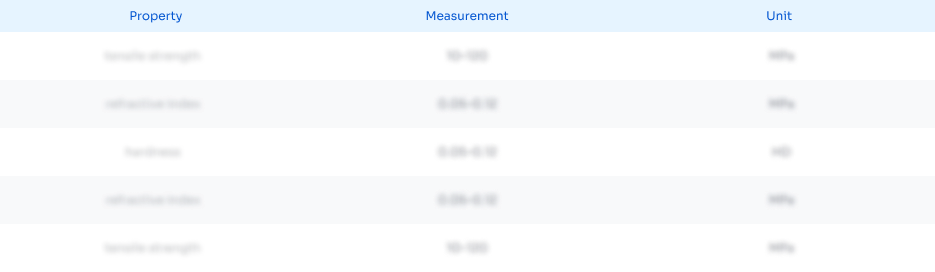
Abstract
Description
Claims
Application Information

- Generate Ideas
- Intellectual Property
- Life Sciences
- Materials
- Tech Scout
- Unparalleled Data Quality
- Higher Quality Content
- 60% Fewer Hallucinations
Browse by: Latest US Patents, China's latest patents, Technical Efficacy Thesaurus, Application Domain, Technology Topic, Popular Technical Reports.
© 2025 PatSnap. All rights reserved.Legal|Privacy policy|Modern Slavery Act Transparency Statement|Sitemap|About US| Contact US: help@patsnap.com