One-time forming process of cold heading for multi-step bushings for vehicles
A molding process and multi-step technology, applied in the direction of metal processing equipment, etc., can solve the problems of increasing the difficulty of one-time molding, the complexity of the mold structure, and the difficulty of drilling holes, so as to save raw materials, increase labor productivity, and improve mechanical properties. Effect
- Summary
- Abstract
- Description
- Claims
- Application Information
AI Technical Summary
Problems solved by technology
Method used
Image
Examples
Embodiment Construction
[0042]In order to make the technical means, creative features, objectives and effects achieved by the present invention easy to understand, the present invention will be further elaborated below.
[0043] see Figure 1 to Figure 8 The one-time forming process of cold heading of multi-step bushing for vehicles includes the following steps:
[0044] Step 1: Cutting the wire: the wire wheel mechanism pulls in the wire, passes through the wire mold, holds the wire against the mountain for positioning, the material cutting mechanism moves, cuts the wire according to the size, and the transmission mechanism clamps the cut material, and sends it to the specific position of the 1# mold , at this time the workpiece is a cylindrical shear.
[0045] combine figure 2 As shown, step 2: Upsetting the cut material and drilling guide holes, the punching unit moves as a whole, the punch rod of the die pushes the workpiece into the cavity of the main mold, the punch rod makes guide holes on ...
PUM
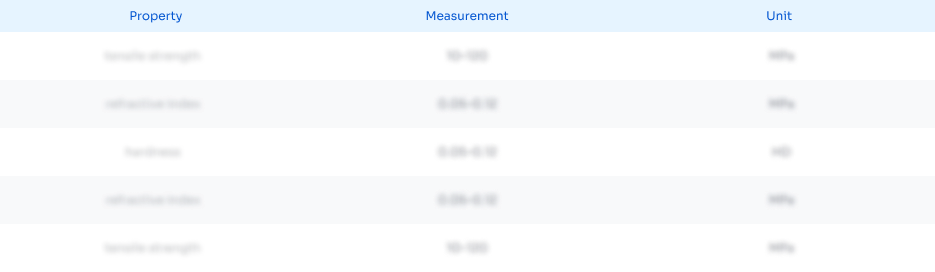
Abstract
Description
Claims
Application Information

- Generate Ideas
- Intellectual Property
- Life Sciences
- Materials
- Tech Scout
- Unparalleled Data Quality
- Higher Quality Content
- 60% Fewer Hallucinations
Browse by: Latest US Patents, China's latest patents, Technical Efficacy Thesaurus, Application Domain, Technology Topic, Popular Technical Reports.
© 2025 PatSnap. All rights reserved.Legal|Privacy policy|Modern Slavery Act Transparency Statement|Sitemap|About US| Contact US: help@patsnap.com