Low-temperature resistant high-resilience rubber windshield material, preparation method thereof and windshield
A technology with low temperature resistance and high resilience, which is applied in the field of windshield, low temperature resistant and high resilience rubber windshield material, which can solve the problems that the windshield capsule cannot return to its original shape in time, poor flexibility, and low self-strength, so as to improve the ozone resistance. Crack performance, improvement of low temperature performance and fatigue performance, and reduction of adverse effects
- Summary
- Abstract
- Description
- Claims
- Application Information
AI Technical Summary
Problems solved by technology
Method used
Image
Examples
Embodiment 1
[0043] The components and mass parts of the low-temperature, high-resilience and long-life flame-retardant and environmentally friendly light-colored rubber windshield material in this embodiment are: EPDM, 75 parts; EPDM, 25 parts; Liquid B Propylene rubber, 8 parts; maleic anhydride modified polybutadiene (commercially available), 8 parts; zinc oxide, 5 parts; stearic acid, 1 part; modified silica, 20 parts; amine salt modified compound Flame retardant, 35 parts; Dicumyl peroxide, 1.5 parts; Sulfur, 0.3 parts; N,N'-m-phenylene polymaleimide, 0.7 parts; Triallyl isocyanurate, 0.9 parts; N,N,N-tetraisobutylthiuram sulfide, 0.9 parts; titanium dioxide, 10 parts, trioctyl phosphate, 4 parts; dioctyl adipate, 3 parts.
[0044] The preparation process is as follows: first add raw rubber in an open mill, mix for 1.5 minutes at 60°C, then pass 4 times, mix well, add amine salt modified composite flame retardant at 130°C, mix Mix for 3.5 minutes; then add modified white carbon black an...
Embodiment 2
[0048] The components and mass parts of the low-temperature, high-resilience and long-life flame-retardant and environmentally friendly light-colored rubber windshield material of this embodiment are: EPDM 60; EPDM 40; liquid ethylene propylene rubber , 10 parts; maleic anhydride modified polybutadiene, 6 parts; zinc oxide, 5 parts; stearic acid, 1 part; modified white carbon black, 30 parts; amine salt modified composite flame retardant, 42 parts ; Trioctyl phosphate, 5 parts; Dioctyl adipate, 4 parts; Dicumyl peroxide, 1.2 parts; Sulfur, 0.3 parts; N,N'-m-phenylene polymaleimide, 0.6 Parts; triallyl isocyanurate, 0.9 parts; N,N,N-tetraisobutylthiuram sulfide, 0.75 parts; dicaprolactam disulfide, 0.5 parts, titanium dioxide, 10 parts.
[0049] The preparation process is as follows: first add raw rubber in an open mill, mix for 1.5 minutes at 60°C, then pass 5 times, mix well, add amine salt modified composite flame retardant at 135°C, mix Mix for 2.5 minutes; then add modified ...
Embodiment 3
[0053] The components and mass parts of the low-temperature resistant, high-resilience and long-life flame-retardant and environmentally friendly light-colored rubber windshield material in this embodiment are: EPDM 50; EPDM 50; liquid ethylene propylene rubber , 12 parts; maleic anhydride modified polybutadiene, 6 parts; zinc oxide, 5 parts; stearic acid, 1 part; modified white carbon black, 25 parts; amine salt modified composite flame retardant, 49 parts ; Trioctyl phosphate, 5 parts; Dioctyl adipate, 4 parts; Dicumyl peroxide, 2.5 parts; Sulfur, 0.4 parts; N,N'-m-phenylene polymaleimide, 0.6 Parts; triallyl isocyanurate, 0.6 parts; N,N,N-tetraisobutylthiuram sulfide, 0.8 parts; dicaprolactam disulfide, 0.4 parts, titanium dioxide, 10 parts.
[0054] The preparation process is: first add raw rubber in an open mill, mix for 1.5 minutes at 60°C, then pass 4 times, mix well, add amine salt modified composite flame retardant at 125°C, mix Mix for 3.5 minutes; then add modified si...
PUM
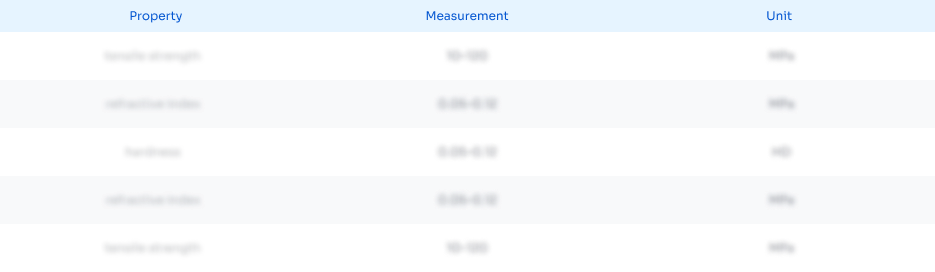
Abstract
Description
Claims
Application Information

- R&D
- Intellectual Property
- Life Sciences
- Materials
- Tech Scout
- Unparalleled Data Quality
- Higher Quality Content
- 60% Fewer Hallucinations
Browse by: Latest US Patents, China's latest patents, Technical Efficacy Thesaurus, Application Domain, Technology Topic, Popular Technical Reports.
© 2025 PatSnap. All rights reserved.Legal|Privacy policy|Modern Slavery Act Transparency Statement|Sitemap|About US| Contact US: help@patsnap.com