Gear box additional damping noise reduction method based on modal strain energy
A modal strain energy and additional damping technology, applied in the field of mechanical shock absorption, can solve the problems that the optimal design of the additional restraint damping structure is not systematic and effective, the design method for fast and effective noise reduction, and the structural load situation is not considered, etc. Achieve the effect of good practicability, good noise reduction effect and clear noise reduction design
- Summary
- Abstract
- Description
- Claims
- Application Information
AI Technical Summary
Problems solved by technology
Method used
Image
Examples
Embodiment 1
[0031] Such as figure 1 As shown, one embodiment of the present invention is based on the design method of additional damping and vibration reduction of gearboxes with structural sound intensity, including the following steps:
[0032] S1, such as figure 2 as shown in image 3 As shown, a gearbox with a size of 652mm×364mm×527mm is established in the ANSYS software and the material is steel. The Solid187 unit is used to divide the mesh of the gearbox, and the mesh size is set to 12mm to obtain the finite element model of the gearbox. The box model is used for modal analysis, the modal analysis data is extracted, and the modal strain energy of each order is solved in Matlab;
[0033] S2, such as image 3 As shown, the modal participation factors of each field point under the excitation frequency can be seen to be negligible after the 21st order. According to the modal strain energy of each order extracted in the modal analysis, the modal damping ratio.
[0034] S3. The bo...
Embodiment 2
[0045] On the basis of Example 1, change the scheme of additional damping according to step S6 in Example 1, and re-solve the radiation noise after additional damping, as Figure 8 As shown, that is to verify the influence of the ratio of the damping layer to the total thickness of the structure on the noise reduction effect. The ratio of the thickness, the obtained point noise at the top of the gearbox when the ratio of different damping layers to the total thickness of the structure is shown in Table 3.
[0046] Table 3 Noise at site 1 on the top of the gearbox under different ratios of the damping layer to the total thickness of the structure
[0047]
[0048]
[0049] Combined with Table 3, the noise at the top field point 1 of the gearbox under the condition of different ratios of the damping layer to the total thickness of the structure is plotted as Figure 8 , when the total thickness of the structure is 48mm, the noise reduction effect is the best when the damp...
Embodiment 3
[0051]On the basis of Example 1, change the scheme of additional damping according to step S6 in Example 1, and re-solve the radiation noise after additional damping, as Figure 9 As shown, that is to verify the effect of the ratio of the additional constrained damping layer to the thickness of the base layer on the noise reduction effect. Select the thickness of the additional constrained damping layer to be 0.75 times (9mm) to 4 times (48mm) the thickness of the base layer, determine the parameters of the damping structure, change the ratio of the additional constrained damping layer to the thickness of the base layer, and obtain different additional constrained damping The noise of the field point 1 on the top of the gearbox when the ratio of the thickness of the layer to the base layer is shown in Table 4:
[0052] Table 4 The noise at site 1 on the top of the gearbox when the ratio of the additional constrained damping layer to the thickness of the base layer is different...
PUM
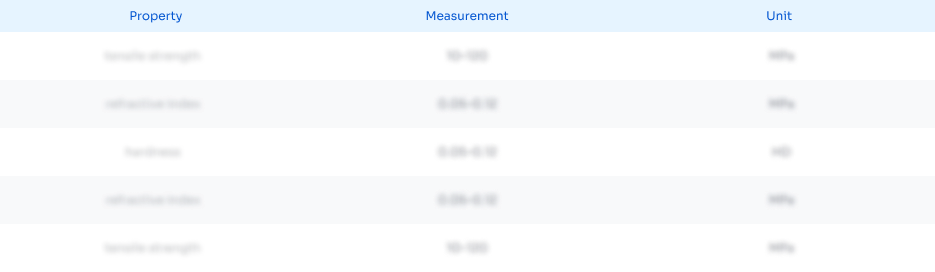
Abstract
Description
Claims
Application Information

- R&D
- Intellectual Property
- Life Sciences
- Materials
- Tech Scout
- Unparalleled Data Quality
- Higher Quality Content
- 60% Fewer Hallucinations
Browse by: Latest US Patents, China's latest patents, Technical Efficacy Thesaurus, Application Domain, Technology Topic, Popular Technical Reports.
© 2025 PatSnap. All rights reserved.Legal|Privacy policy|Modern Slavery Act Transparency Statement|Sitemap|About US| Contact US: help@patsnap.com