Hub extrusion forming method
A technology of extrusion forming and wheel hub, applied in the direction of wheels, transportation and packaging, metal processing equipment, etc., can solve the problems of complex forming equipment, reduced material utilization rate, increased production cost, etc., to achieve a simple and easy forming process, improve material Utilization rate, the effect of saving production costs
- Summary
- Abstract
- Description
- Claims
- Application Information
AI Technical Summary
Problems solved by technology
Method used
Image
Examples
Embodiment
[0029] A hub extrusion forming method. Taking a magnesium alloy wheel hub whose material is AZ80 as an example, the process of manufacturing the wheel hub by adopting the wheel hub extrusion forming method of the present invention is divided into two parts: the pre-forging forming of the rim and the inner rim and the final forging forming of the spoke and the outer rim .
[0030] Pre-forging forming process: 1. Obtain a cylindrical cake-shaped magnesium alloy billet, put the billet into a heating furnace to heat at 300-450°C, and keep it warm for a period of time; 2. Put the preheated billet flat into the pre-forging mold cavity place them together on the workbench of the hydraulic press, push the pre-forging upper punch 2 to extrude downward, and back-extrude to obtain the complete pre-forged wheel blank with the rim and inner rim of the wheel hub, and obtain the pre-forged wheel blank after simple processing Such as Figure 7 shown;
[0031] Final forging forming process:...
PUM
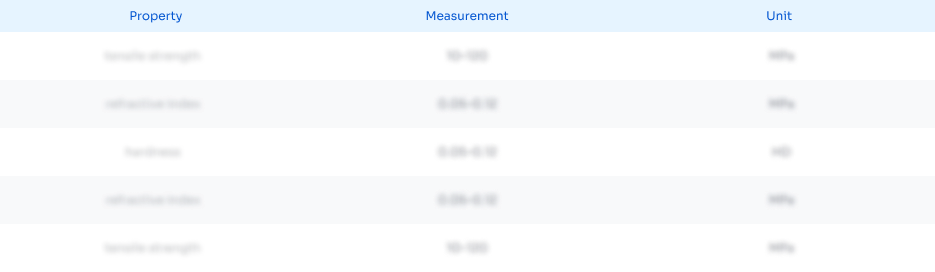
Abstract
Description
Claims
Application Information

- R&D
- Intellectual Property
- Life Sciences
- Materials
- Tech Scout
- Unparalleled Data Quality
- Higher Quality Content
- 60% Fewer Hallucinations
Browse by: Latest US Patents, China's latest patents, Technical Efficacy Thesaurus, Application Domain, Technology Topic, Popular Technical Reports.
© 2025 PatSnap. All rights reserved.Legal|Privacy policy|Modern Slavery Act Transparency Statement|Sitemap|About US| Contact US: help@patsnap.com