A method and system for rotating fixed-bed residual oil hydrotreating
A hydrogenation treatment and hydrogenation pretreatment technology, which is applied in the fields of hydrogenation treatment process, hydrocarbon oil treatment, petroleum industry, etc., can solve the problems of insufficient scale and impurity capacity, increased heating furnace load, low proportion of protective agent, etc. Achieve the effects of stable operation, slow down the deactivation rate, and stable material properties
- Summary
- Abstract
- Description
- Claims
- Application Information
AI Technical Summary
Problems solved by technology
Method used
Image
Examples
Embodiment 1
[0051] This embodiment adopts as figure 1The reaction system shown includes a first hydrotreating reactor 1, a second hydrotreating reactor 2, a third hydrotreating reactor 3, a hydrotreating reactor 5, and a hydrotreating reactor 6 , Hydrotreating reactor 7. The main reaction feed pipeline L1 is respectively connected to the inlets of the first hydrogenation pretreatment reactor 1, the second hydrogenation pretreatment reactor 2, and the third hydrogenation pretreatment reactor 3 through three inlet pipelines. The inlet pipelines are all equipped with inlet valve bodies, that is, the main reaction feed pipeline L1 passes through the valve body 21, the valve body 22, and the valve body 23 to connect with the first hydrogenation pretreatment reactor 1 and the second hydrogenation pretreatment reactor 2 respectively. , The inlet of the third hydrogenation pretreatment reactor 3 is connected; The reaction discharge main pipeline L2 is connected with the first hydrogenation pretr...
Embodiment 2
[0076] This example is basically the same as Example 1, except that the raw material is residual oil B, the properties of the specific raw material are shown in Table 1, the reaction temperature and switching time of the hydrogenation pre-reactor are shown in Table 4 and Table 5, and the residual oil is hydrogenated to form See Table 6 for oil properties.
[0077] The reaction condition of hydrogenation pretreatment reaction zone in the embodiment 2 of table 4
[0078]
[0079] The switching time of hydrogenation pretreatment reactor in the embodiment 2 of table 5
[0080] switch for the first time second switch switch for the third time fourth switch switching time, h 6500 9400 11900 13750
Embodiment 3
[0082] This example adopts the reaction system, reaction raw materials and reactor rotation method of Example 1, the difference is: the first hydrogenation pretreatment reactor 1, the second hydrogenation pretreatment reactor 2, the third hydrogenation pretreatment The ratio of demetallization agent to protective agent in reactor 3 is 1:1, and remains unchanged for each rotation. The switching time of the hydrogenation pretreatment reactor is shown in Table 6.
[0083] In Example 3, due to the deactivation of the hydrotreating catalyst and the pressure drop of the reactor in the main reaction zone reached the design value, the operation was forced to shut down. The operating cycle is shown in Table 7.
[0084] The switching time of hydrogenation pretreatment reactor in the embodiment 3 of table 6
[0085] switch for the first time second switch switch for the third time fourth switch switching time, h 5000 7300 9000 10500
PUM
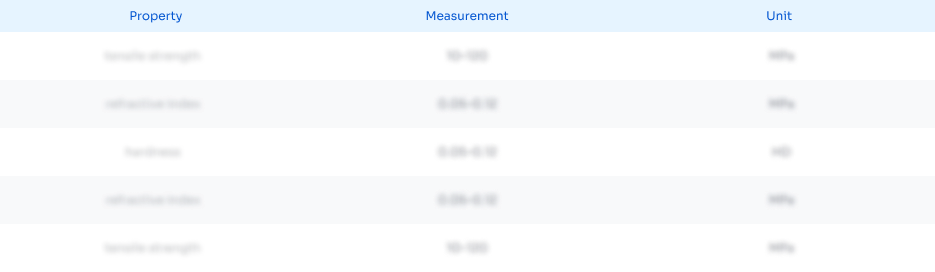
Abstract
Description
Claims
Application Information

- R&D
- Intellectual Property
- Life Sciences
- Materials
- Tech Scout
- Unparalleled Data Quality
- Higher Quality Content
- 60% Fewer Hallucinations
Browse by: Latest US Patents, China's latest patents, Technical Efficacy Thesaurus, Application Domain, Technology Topic, Popular Technical Reports.
© 2025 PatSnap. All rights reserved.Legal|Privacy policy|Modern Slavery Act Transparency Statement|Sitemap|About US| Contact US: help@patsnap.com