Microchannel radiator for air conditioner
A radiator, micro-channel technology, applied in indirect heat exchangers, heat exchanger types, heat exchange equipment, etc., can solve the problem of no natural cooling porous structure, air can not flow, etc.
- Summary
- Abstract
- Description
- Claims
- Application Information
AI Technical Summary
Problems solved by technology
Method used
Image
Examples
preparation example Construction
[0034] The preparation method of heat-dissipating coating, it comprises:
[0035] The first step is the preparation of graphene by electrical treatment. Fill the graphene powder in the hollow graphene rod, use the graphene rod as the cathode and anode, assemble it into the reaction chamber of the arc equipment with a fixture, and remove the air in the arc discharge reaction chamber , filled with a mixture of high-purity helium and hydrogen, connected to a DC power supply to discharge, and obtained electrically-treated graphene;
[0036] In the second step, the preparation of silicon oxide nanofiber spinning solution, tetraethyl silicate is dissolved in the mixed solution formed by hydrochloric acid solution and ethanol solution, and polyvinylpyrrolidone is dissolved in isopropanol and N,N-dimethylformaldehyde In the mixed solution formed by amides, mix the two spinning solutions evenly to form a homogeneous solution;
[0037] The third step, the preparation of electrically tr...
Embodiment 1
[0047] Embodiment 1 Preparation of electrically treated graphene
[0048] 1g of graphene powder is filled in a hollow graphene rod with a diameter of 6 mm and a length of 15 cm. The graphene rod is used as the negative and positive poles, assembled into the reaction chamber of the discharge device with a clamp, and after the air in the discharge reaction chamber is removed, it is filled with The mixed gas of high-purity helium and hydrogen, the pressure is 500Torr, the flow rate of hydrogen and helium is 400sccm, and the DC power supply is connected to discharge at a current of 150A to obtain graphene.
Embodiment 2
[0049] Example 2 Preparation of electro-treated graphene / silicon oxide nanofibers
[0050] 1.5g tetraethyl silicate is dissolved in the mixed solution that 0.6g hydrochloric acid solution and 0.4g ethanol solution form, and 1.1g polyvinylpyrrolidone is dissolved in 4.9g isopropanol and 8.2gN, N-dimethylformamide forms In the mixed solution, the two spinning solutions are mixed uniformly to form a homogeneous solution; the electro-treated graphene prepared in Example 1 is added to the prepared electro-treated graphene / silicon oxide nanofiber material according to the weight ratio of 15% of the formed electro-treated graphene / silicon oxide nanofiber material. In a homogeneous solution, stir at a temperature of 60°C for 12 hours, put it into an electrospinning device, and conduct electrospinning under the conditions of a voltage of 15kV and a receiving distance of about 10cm. After 9 hours, the product is collected, and then the product is placed in a vacuum oven Dry in medium fo...
PUM
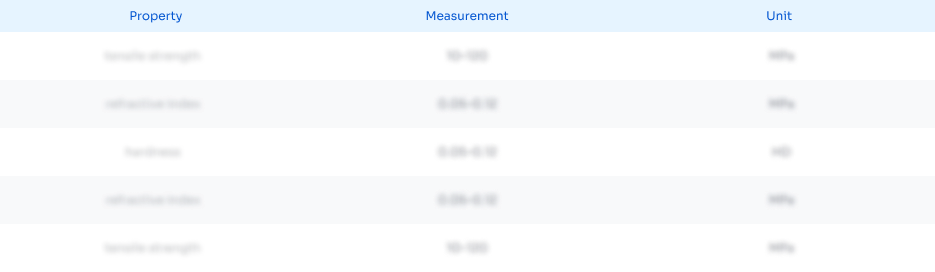
Abstract
Description
Claims
Application Information

- R&D
- Intellectual Property
- Life Sciences
- Materials
- Tech Scout
- Unparalleled Data Quality
- Higher Quality Content
- 60% Fewer Hallucinations
Browse by: Latest US Patents, China's latest patents, Technical Efficacy Thesaurus, Application Domain, Technology Topic, Popular Technical Reports.
© 2025 PatSnap. All rights reserved.Legal|Privacy policy|Modern Slavery Act Transparency Statement|Sitemap|About US| Contact US: help@patsnap.com