Reverse visual collimator
A collimator and reverse technology, applied in the direction of optics, optical components, measuring devices, etc., can solve the problems of eyepiece fatigue reading, low accuracy, instrument accuracy error, etc., to avoid human eye fatigue and danger, and save occupancy The effect of improving ground space and area, accuracy and uniformity
- Summary
- Abstract
- Description
- Claims
- Application Information
AI Technical Summary
Problems solved by technology
Method used
Image
Examples
Embodiment Construction
[0014] In order to have a clearer understanding of the technical features, objectives and effects of the invention, the specific embodiments of the invention will now be described with reference to the accompanying drawings. In each figure, the same reference numerals represent the same components. In order to make the drawings concise, each figure only schematically shows the parts related to the present invention, and they do not represent the actual structure of the product as a product.
[0015] Such as figure 1 , 2 As shown, the present invention is an anti-visible collimator, including a collimator 11, the collimator 11 includes a laser display part, an optical display part and an optical part, the laser display part and the optical part are arranged on a horizontal line, The optical display part is vertically arranged between the laser display part and the optical part. The middle part of the collimator 11 is symmetrically provided with two collimator integrated fine-tuning...
PUM
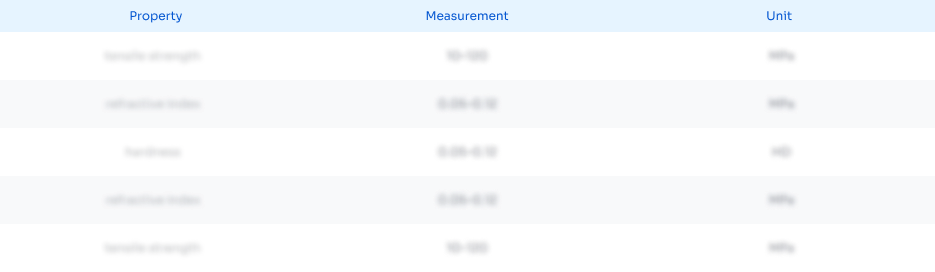
Abstract
Description
Claims
Application Information

- R&D
- Intellectual Property
- Life Sciences
- Materials
- Tech Scout
- Unparalleled Data Quality
- Higher Quality Content
- 60% Fewer Hallucinations
Browse by: Latest US Patents, China's latest patents, Technical Efficacy Thesaurus, Application Domain, Technology Topic, Popular Technical Reports.
© 2025 PatSnap. All rights reserved.Legal|Privacy policy|Modern Slavery Act Transparency Statement|Sitemap|About US| Contact US: help@patsnap.com