Alignment method of multi-pole magnet based on three-coordinate measuring machine
A three-coordinate measuring machine and magnet technology, which is applied to the measuring device, the size/direction of the magnetic field, and the direction of the instrument, etc., can solve the problems such as the collimation accuracy cannot meet the requirements, the time-consuming time, and the difficulty of the magnet processing and manufacturing the high-precision magnetic field quality.
- Summary
- Abstract
- Description
- Claims
- Application Information
AI Technical Summary
Problems solved by technology
Method used
Image
Examples
Embodiment Construction
[0029] The application will be further described in detail below in conjunction with the accompanying drawings and embodiments. It should be understood that the specific embodiments described here are only used to explain related inventions, rather than to limit the invention. It should also be noted that, for ease of description, only parts related to the invention are shown in the drawings.
[0030] It should be noted that, in the case of no conflict, the embodiments in the present application and the features in the embodiments can be combined with each other. The present application will be described in detail below with reference to the accompanying drawings and embodiments.
[0031] In order to measure the magnetic field quality of the multi-pole magnet, the multi-pole magnet to be tested is excited, and the induction signal is obtained by the change of the magnetic flux induced by the sensor, and the magnetic field quality is obtained by analyzing the induction signal....
PUM
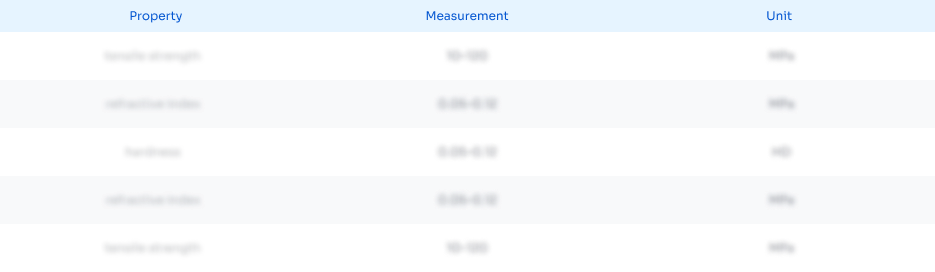
Abstract
Description
Claims
Application Information

- R&D Engineer
- R&D Manager
- IP Professional
- Industry Leading Data Capabilities
- Powerful AI technology
- Patent DNA Extraction
Browse by: Latest US Patents, China's latest patents, Technical Efficacy Thesaurus, Application Domain, Technology Topic, Popular Technical Reports.
© 2024 PatSnap. All rights reserved.Legal|Privacy policy|Modern Slavery Act Transparency Statement|Sitemap|About US| Contact US: help@patsnap.com