Plastic tube hot-melting welding machine
A technology for plastic pipes and welding machines, applied in the field of plastics, can solve the problems of welding failure, defective products, and inability to heat at the same time.
- Summary
- Abstract
- Description
- Claims
- Application Information
AI Technical Summary
Problems solved by technology
Method used
Image
Examples
Embodiment Construction
[0045] like figure 1 , 2 As shown, it includes installation shell 1, return spring 2, hot melt block 3, drive arm 4, limit plate 5, guide block 6, drive mechanism 7, trigger mechanism 8, drive swing rod 10, threaded rod 18, guide rod 12, guide groove 15, T-shaped slide block 31, drive plate 49, drive spring 19, slide block 20, wherein as Figure 7 As shown, there is a threaded hole 28 on the installation shell 1, such as Image 6 As shown, the threaded rod 18 is installed on the fixed shell through the threaded hole 28, and the two ends of the threaded rod 18 pass through the mounting shell 1 and are located on both sides of the mounting shell 1; Figure 5 As shown, one end of the driving arm 4 has a detachable fixing ring 11 for fixing the plastic pipe, and the other end of the driving arm 4 is installed on the two ends of the threaded rod 18 through screw fit; one side of the driving arm 4 is equipped with a guide rod 12, like Figure 4 As shown, there are two through gu...
PUM
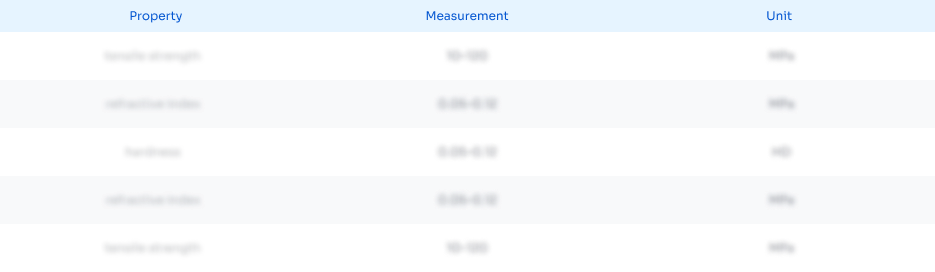
Abstract
Description
Claims
Application Information

- R&D Engineer
- R&D Manager
- IP Professional
- Industry Leading Data Capabilities
- Powerful AI technology
- Patent DNA Extraction
Browse by: Latest US Patents, China's latest patents, Technical Efficacy Thesaurus, Application Domain, Technology Topic, Popular Technical Reports.
© 2024 PatSnap. All rights reserved.Legal|Privacy policy|Modern Slavery Act Transparency Statement|Sitemap|About US| Contact US: help@patsnap.com