Super-hydrophobic nano-cellulose membrane and preparation method thereof
A nano-cellulose, super-hydrophobic technology, applied in the direction of coating, etc., can solve the problems of limitations, mechanical properties of pure cellulose membrane materials, poor hydrophobicity, etc., and achieve the effect of low cost, high strength, and simple preparation process
- Summary
- Abstract
- Description
- Claims
- Application Information
AI Technical Summary
Problems solved by technology
Method used
Examples
Embodiment 1
[0037] (1) Prepare film with cellulose nanocellulose:
[0038] ① Preparation of film-forming liquid: 0.5 parts of cellulose nanofibers, 99.5 parts of distilled water, blending and stirring for 5 minutes, ultrasonic dispersion to obtain film-forming liquid, ultrasonic power 600W, dispersion time 20 minutes;
[0039] ②Film preparation: pour the film-forming solution obtained in step ① onto the film-forming device to cast and dry to form a film. The film-forming condition temperature is 40°C, relative humidity is 40%, and the time is 24h;
[0040] ③Put the dried nanocellulose membrane into a 57% desiccator to balance for 3 days.
[0041] (2) modifying the nano-silica to obtain a super-hydrophobic nano-silica solution:
[0042] ① Blend 3 parts of nano-silica, 2 parts of modifier, and 100 parts of dispersant;
[0043] ②Put the mixed solution obtained in step ① into a water bath at a certain temperature to stir, the stirring temperature is 60° C., and the stirring time is 8 hours....
Embodiment 2
[0050] (1) Prepare film with cellulose nanocellulose:
[0051] ① Preparation of film-forming liquid: 0.5 parts of cellulose nanofibers, 99.5 parts of distilled water, blending and stirring for 5 minutes, ultrasonic dispersion to obtain film-forming liquid, ultrasonic power 600W, dispersion time 20 minutes;
[0052]②Film preparation: pour the film-forming solution obtained in step ① onto the film-forming device to cast and dry to form a film. The film-forming condition temperature is 45°C, relative humidity is 45%, and the time is 24h;
[0053] ③Put the dried nanocellulose membrane into a 57% desiccator to balance for 4 days.
[0054] (2) modifying the nano-silica to obtain a super-hydrophobic nano-silica solution:
[0055] ① Blend 4 parts of nano-silica, 3 parts of modifier, and 102 parts of dispersant;
[0056] ②Put the mixed solution obtained in step ① into a water bath at a certain temperature and stir, the stirring temperature is 60° C., and the stirring time is 10 h.
...
Embodiment 3
[0063] (1) Prepare film with cellulose nanocellulose:
[0064] ① Preparation of film-forming liquid: 0.5 parts of cellulose nanofibers, 99.5 parts of distilled water, blending and stirring for 5 minutes, ultrasonic dispersion to obtain film-forming liquid, ultrasonic power 600W, dispersion time 20 minutes;
[0065] ②Film preparation: pour the film-forming solution obtained in step ① onto the film-forming device to cast and dry to form a film. The film-forming condition temperature is 50°C, relative humidity is 50%, and the time is 24 hours;
[0066] ③Put the dried nanocellulose membrane into a 57% desiccator to balance for 3 days.
[0067] (2) modifying the nano-silica to obtain a super-hydrophobic nano-silica solution:
[0068] ① Blend 3 parts of nano-silica, 2 parts of modifier, and 100 parts of dispersant;
[0069] ②Put the mixed solution obtained in step ① into a water bath at a certain temperature to stir, the stirring temperature is 60° C., and the stirring time is 8 h...
PUM
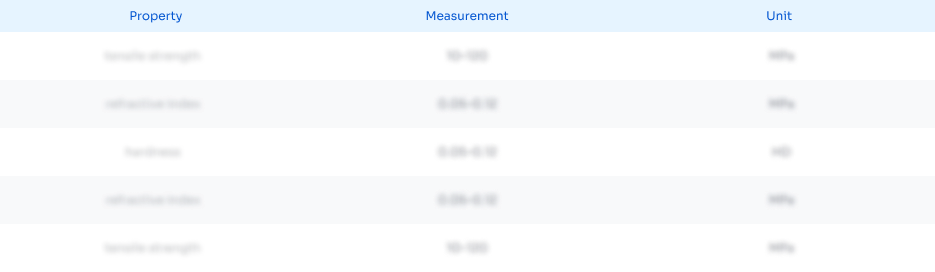
Abstract
Description
Claims
Application Information

- R&D Engineer
- R&D Manager
- IP Professional
- Industry Leading Data Capabilities
- Powerful AI technology
- Patent DNA Extraction
Browse by: Latest US Patents, China's latest patents, Technical Efficacy Thesaurus, Application Domain, Technology Topic, Popular Technical Reports.
© 2024 PatSnap. All rights reserved.Legal|Privacy policy|Modern Slavery Act Transparency Statement|Sitemap|About US| Contact US: help@patsnap.com