Thin-wall part robot machining path generation method based on machining parameters
A technology for robot processing and thin-walled parts, applied in the direction of instruments, digital control, program control, etc., can solve the problems of calculating the machining allowance from the design model and restricting the application of robots, etc. Effect
- Summary
- Abstract
- Description
- Claims
- Application Information
AI Technical Summary
Problems solved by technology
Method used
Image
Examples
Embodiment Construction
[0036] In order to make the object, technical solution and advantages of the present invention clearer, the present invention will be further described in detail below in conjunction with the accompanying drawings and embodiments. It should be understood that the specific embodiments described here are only used to explain the present invention, not to limit the present invention. In addition, the technical features involved in the various embodiments of the present invention described below can be combined with each other as long as they do not constitute a conflict with each other.
[0037] see figure 1 , figure 2 and image 3 , the method for generating a machining path of a thin-walled part robot based on processing parameters provided by the present invention, the method is suitable for the generation of a milling path for a small-curvature thin-walled part, which includes the following steps:
[0038] Step 1, collecting the three-dimensional shape measuring point dat...
PUM
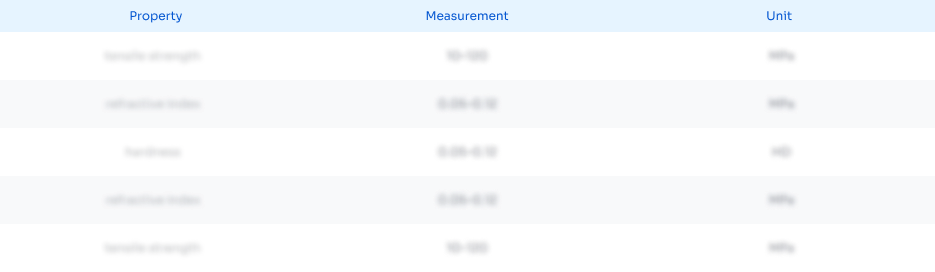
Abstract
Description
Claims
Application Information

- R&D
- Intellectual Property
- Life Sciences
- Materials
- Tech Scout
- Unparalleled Data Quality
- Higher Quality Content
- 60% Fewer Hallucinations
Browse by: Latest US Patents, China's latest patents, Technical Efficacy Thesaurus, Application Domain, Technology Topic, Popular Technical Reports.
© 2025 PatSnap. All rights reserved.Legal|Privacy policy|Modern Slavery Act Transparency Statement|Sitemap|About US| Contact US: help@patsnap.com