Method for improving low-frequency vibration performance of complex structure
A low-frequency vibration and complex structure technology, applied in special data processing applications, instruments, electrical digital data processing, etc., can solve problems such as low-frequency vibration
- Summary
- Abstract
- Description
- Claims
- Application Information
AI Technical Summary
Problems solved by technology
Method used
Image
Examples
Embodiment Construction
[0033] The flow process that the inventive method realizes is as figure 1 Shown:
[0034] Step 1: Experimental Modal Analysis
[0035] Build a test platform, and use the test modal analysis method to obtain the test structure modal and vibration frequency response functions of the automobile body structure;
[0036] Step 2: Build a CAE simulation analysis model
[0037] Finite element modeling technology builds the finite element analysis model of the body structure, performs finite element simulation analysis, and obtains the simulated structural mode and vibration frequency response function;
[0038] Step 3: Modal benchmarking
[0039] Based on the actual body structure and test mode, conduct modal benchmarking analysis to confirm the accuracy and reliability of the finite element model;
[0040] Step 4: Sensitivity Analysis
[0041] Based on the finite element model completed by benchmarking, for the abnormal frequency of the peak value of the vibration frequency resp...
PUM
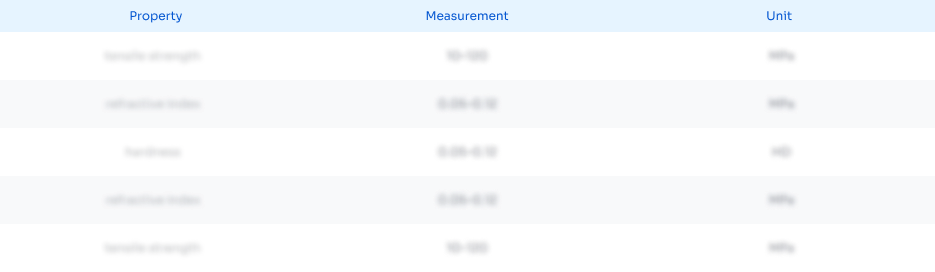
Abstract
Description
Claims
Application Information

- R&D
- Intellectual Property
- Life Sciences
- Materials
- Tech Scout
- Unparalleled Data Quality
- Higher Quality Content
- 60% Fewer Hallucinations
Browse by: Latest US Patents, China's latest patents, Technical Efficacy Thesaurus, Application Domain, Technology Topic, Popular Technical Reports.
© 2025 PatSnap. All rights reserved.Legal|Privacy policy|Modern Slavery Act Transparency Statement|Sitemap|About US| Contact US: help@patsnap.com