Airport runway crack detection and maintenance equipment
A technology for airport runways and maintenance equipment, applied in road repair, roads, roads, etc., can solve problems such as performance degradation, damage to pavement structure, and difficulty in viewing crack depth, and achieve a good crack repair effect.
- Summary
- Abstract
- Description
- Claims
- Application Information
AI Technical Summary
Problems solved by technology
Method used
Image
Examples
Embodiment 1
[0038] Embodiment 1, airport runway crack detection and maintenance equipment, including a trailer 1 and a tractor connected to the front of the trailer 1, it is characterized in that the upper end surface of the trailer 1 is longitudinally spaced and provided with a slider 2 that is slidably connected to the trailer 1 and slides Slider 3 is vertically slidably connected in cylinder 2, and described slider 2 is driven by the first driving device that is arranged on the upper end surface of trailer 1, and two sliders 2 upper ends are provided with vertically extending horizontal bar 5 and two sliders 3 are placed The outer end of the sliding cylinder 2 is respectively connected to the longitudinal sides of the crossbar 5, the lower end of the crossbar 5 is fixedly connected with a crack detection device and the crack detection device is electrically connected to a micro-controller processor, and the slide rod 3 is connected with it. A first return spring 6 is connected between t...
Embodiment 2
[0043]Embodiment 2, on the basis of Embodiment 1, rectangular sliding chambers 13 are respectively opened on the longitudinal side walls of the detection hole 7 and the protective plate 8 is slidably connected in the rectangular sliding chamber 13. The trigger device includes: The protective plate 8 is placed on the first conductive sheet on the side wall of the rectangular sliding cavity 13 and the bottom wall of the rectangular sliding cavity 13 is provided with a second conductive sheet matching the first conductive sheet, and the positioning device includes: the sliding cylinder 2 An electromagnet is provided on the inner bottom wall, and the electromagnet is connected in series with the first conductive sheet and the second conductive sheet in the voltage stabilizing circuit provided on the trailer 1, and an iron sheet is fixed at the bottom of the slide bar 3.
[0044] When this embodiment is in use, how the trigger device works will be described in detail below; Figure...
Embodiment 3
[0046] Embodiment 3, on the basis of Embodiment 2, a second chamber 14 extending longitudinally and spaced laterally from the two rectangular sliding chambers 13 is provided in the trailer 1 near the end of the cleaning device, and the third driving device includes: Two protective plates 8 are respectively connected with racks 15 at one end close to the cleaning device, and the racks 15 are longitudinally slidably connected in the second cavity 14, and the two racks 15 are jointly meshed with a gear 16 arranged in the second cavity 14 and The gear 16 is driven by an opening and closing motor 17 disposed in the second cavity 14 .
[0047] When this embodiment is in use, what constitutes about the third driving device and how to drive the two protective plates 8 to move will be described in detail below; Figure 10 , 15 As shown, two protective plates 8 are respectively connected with racks 15 near the ends of the cleaning device, and the racks 15 are longitudinally slidably co...
PUM
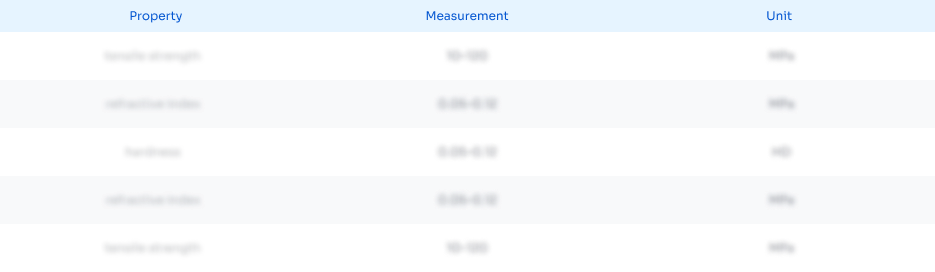
Abstract
Description
Claims
Application Information

- Generate Ideas
- Intellectual Property
- Life Sciences
- Materials
- Tech Scout
- Unparalleled Data Quality
- Higher Quality Content
- 60% Fewer Hallucinations
Browse by: Latest US Patents, China's latest patents, Technical Efficacy Thesaurus, Application Domain, Technology Topic, Popular Technical Reports.
© 2025 PatSnap. All rights reserved.Legal|Privacy policy|Modern Slavery Act Transparency Statement|Sitemap|About US| Contact US: help@patsnap.com