A workpiece grinding and polishing robot
A technology for robots and workpieces, applied in the field of robots, can solve the problems of continuous movement of workers and uneven grinding, and achieve the effects of saving manpower, uniform grinding, and improving practicability.
- Summary
- Abstract
- Description
- Claims
- Application Information
AI Technical Summary
Problems solved by technology
Method used
Image
Examples
Embodiment 1
[0019] A workpiece grinding and polishing robot, such as Figure 1-3 As shown, it includes a fixed frame 1, a start switch 2, a clamp switch 3, a control box 4, a rotating motor 5, a connecting rod 6, a support rod 7, a clamping device 8, a ring frame 9, a moving rod 11, a triangular block 12, Clamping block 121, grinding rod 13 and grinding block 14, start switch 2 and clamping switch 3 are installed on the left side of the inner bottom wall of fixed frame 1, starting switch 2 is positioned at the left side of clamping switch 3, fixed frame 1 inner bottom wall A control box 4 is installed in the middle, and the control box 4 includes a switching power supply, a power module and a control module. A rotating motor 5 is installed on the left side of the inner bottom wall of the fixed frame 1. The rotating motor 5 is located on the left side of the start switch 2. The output of the rotating motor 5 The left and right sides of the shaft are connected with connecting rods 6, and th...
Embodiment 2
[0021] A workpiece grinding and polishing robot, such as Figure 1-3 As shown, it includes a fixed frame 1, a start switch 2, a clamp switch 3, a control box 4, a rotating motor 5, a connecting rod 6, a support rod 7, a clamping device 8, a ring frame 9, a moving rod 11, a triangular block 12, Clamping block 121, grinding rod 13 and grinding block 14, start switch 2 and clamping switch 3 are installed on the left side of the inner bottom wall of fixed frame 1, starting switch 2 is positioned at the left side of clamping switch 3, fixed frame 1 inner bottom wall A control box 4 is installed in the middle, and the control box 4 includes a switching power supply, a power module and a control module. A rotating motor 5 is installed on the left side of the inner bottom wall of the fixed frame 1. The rotating motor 5 is located on the left side of the start switch 2. The output of the rotating motor 5 The left and right sides of the shaft are connected with connecting rods 6, and th...
Embodiment 3
[0024] A workpiece grinding and polishing robot, such as Figure 1-3As shown, it includes a fixed frame 1, a start switch 2, a clamp switch 3, a control box 4, a rotating motor 5, a connecting rod 6, a support rod 7, a clamping device 8, a ring frame 9, a moving rod 11, a triangular block 12, Clamping block 121, grinding rod 13 and grinding block 14, start switch 2 and clamping switch 3 are installed on the left side of the inner bottom wall of fixed frame 1, starting switch 2 is positioned at the left side of clamping switch 3, fixed frame 1 inner bottom wall A control box 4 is installed in the middle, and the control box 4 includes a switching power supply, a power module and a control module. A rotating motor 5 is installed on the left side of the inner bottom wall of the fixed frame 1. The rotating motor 5 is located on the left side of the start switch 2. The output of the rotating motor 5 The left and right sides of the shaft are connected with connecting rods 6, and the...
PUM
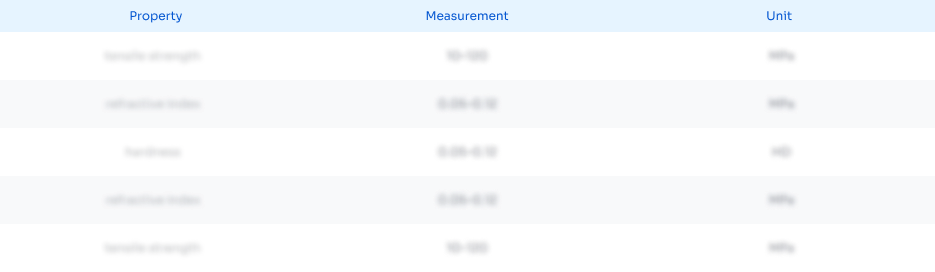
Abstract
Description
Claims
Application Information

- R&D
- Intellectual Property
- Life Sciences
- Materials
- Tech Scout
- Unparalleled Data Quality
- Higher Quality Content
- 60% Fewer Hallucinations
Browse by: Latest US Patents, China's latest patents, Technical Efficacy Thesaurus, Application Domain, Technology Topic, Popular Technical Reports.
© 2025 PatSnap. All rights reserved.Legal|Privacy policy|Modern Slavery Act Transparency Statement|Sitemap|About US| Contact US: help@patsnap.com