Cable Production Plant
A technology for producing devices and cables, applied in the direction of wire drawing dies, etc., can solve the problems of inability to automatically calibrate, scratch the wire core, and the wire core cannot keep the center line of the wire drawing die hole level.
- Summary
- Abstract
- Description
- Claims
- Application Information
AI Technical Summary
Problems solved by technology
Method used
Image
Examples
Embodiment 1
[0038]The first embodiment is basically as attachedfigure 1 Shown: The cable production device includes a motor and a housing 1. The housing 1 also includes a winding mechanism, a positioning and calibration mechanism, and a wire pulling mechanism from left to right. The winding mechanism from top to bottom includes a winding wheel 2 for winding the wire core 5, a base 3 for supporting the winding wheel 2 and a telescopic cylinder 4 for lifting the base 3, the lower end of the telescopic cylinder 4 is fixedly connected by screws At the inner bottom of the housing 1, the upper end of the telescopic cylinder 4 used to push the base 3 up and down is fixedly connected with the bottom of the base 3 by screws. The reel 2 is coaxially connected with a rotating shaft, and the rotating shaft is rotatably connected with the upper end of the base 3. The telescopic cylinder 4 The model is: JB400×S, and the motor model is: Y-180L-8.
[0039]The positioning and calibration mechanism includes a calib...
Embodiment 2
[0048]The second embodiment is basically as attachedFigure 4 As shown, the difference between the second embodiment and the first embodiment is the reel 2 and the base 3. The upper end of the base 3 is provided with a groove for accommodating the reel 2. The reel 2 is hollow inside, the right side is open, and the left The side is closed, and the upper and lower openings on the right side are respectively bonded with arc-shaped magnetic strips 16 matching the shape of the inner wall of the reel 2, and the polarities of the upper and lower arc-shaped magnetic strips 16 are opposite, and the left side of the reel 2 A rotating shaft 15 is fixedly connected coaxially. The rotating shaft 15 passes through the left side wall of the reel 2 and is rotatably connected with the left side wall of the groove of the base 3. The right side wall of the groove is fixedly connected with a fixing rod 18 by screws. 18 Extend from the right side of the reel 2 into the inside of the reel 2, such asFigur...
PUM
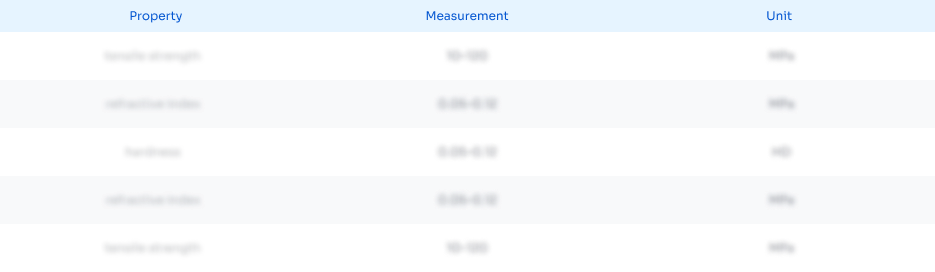
Abstract
Description
Claims
Application Information

- R&D Engineer
- R&D Manager
- IP Professional
- Industry Leading Data Capabilities
- Powerful AI technology
- Patent DNA Extraction
Browse by: Latest US Patents, China's latest patents, Technical Efficacy Thesaurus, Application Domain, Technology Topic, Popular Technical Reports.
© 2024 PatSnap. All rights reserved.Legal|Privacy policy|Modern Slavery Act Transparency Statement|Sitemap|About US| Contact US: help@patsnap.com