A Neural Network Based Output Control Method for Piezoelectric Ceramic Actuators
A piezoelectric ceramic and neural network technology, applied in the field of piezoelectric ceramic driver output control, can solve the problems of inability to install and obtain the output force value of the piezoelectric ceramic driver, and achieve high precision, convenient and fast training, and strong adaptability. Effect
- Summary
- Abstract
- Description
- Claims
- Application Information
AI Technical Summary
Problems solved by technology
Method used
Image
Examples
Embodiment Construction
[0051] The specific embodiments of the present invention will be described in detail below in conjunction with the technical solutions and accompanying drawings.
[0052] attached image 3 It is the data acquisition experiment diagram of the input voltage and output force of the piezoelectric ceramic driver. The piezoelectric ceramic driver is the unpackaged PICA Stack Piezo Actuators P-016.20 high-voltage (1000V) high-voltage output piezoelectric ceramic driver produced by Physik Instrumente Company in Germany; Functional boards, including data acquisition boards and voltage output boards; the signal amplifier is an E-472.20 signal amplifier produced by Physik Instrumente, Germany, with a rated power of 550W; the force sensor is a load cell produced by Honeywell, with up to 0.1% The low error rate can realize the conversion of mechanical measurement units through the virtual instrument LabVIEW software.
[0053] attached Figure 5 It is a flow chart of the piezoelectric ce...
PUM
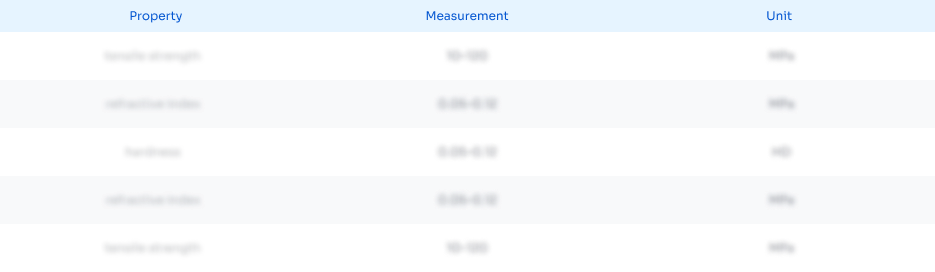
Abstract
Description
Claims
Application Information

- R&D
- Intellectual Property
- Life Sciences
- Materials
- Tech Scout
- Unparalleled Data Quality
- Higher Quality Content
- 60% Fewer Hallucinations
Browse by: Latest US Patents, China's latest patents, Technical Efficacy Thesaurus, Application Domain, Technology Topic, Popular Technical Reports.
© 2025 PatSnap. All rights reserved.Legal|Privacy policy|Modern Slavery Act Transparency Statement|Sitemap|About US| Contact US: help@patsnap.com