A hydraulic compaction method for backfilling bridge and culvert abutments
A bridge and culvert, hydraulic technology, applied in soil protection, construction, infrastructure engineering and other directions, can solve the problems of increasing construction costs, low compaction quality, slow construction progress, etc., to save construction costs, ensure compaction quality, The effect of reducing the amount of construction
- Summary
- Abstract
- Description
- Claims
- Application Information
AI Technical Summary
Problems solved by technology
Method used
Image
Examples
Embodiment 1
[0031] Such as figure 1 As shown, the present invention selects sandy soil and fine-grained soil backfill layer, including the following steps:
[0032] Step 1. Preparation before ramming:
[0033] A1. The construction surface must be leveled with a bulldozer before ramming, and then the road roller is rolled, and the compaction standards and flatness required by the design are inspected. For the construction surface that does not meet the design requirements, repeat leveling and rolling until it meets the design It is required that when the construction surface is relatively dry, an appropriate amount of water should be sprayed to prevent the surface from dusting, which will affect the energy transfer to the deep layer;
[0034] A2. Release the operating points on the construction surface after the inspection is passed. When arranging the operating points, the gap-type operating points are arranged. The gap-type operating points are arranged at 20cm apart from the edge of each opera...
Embodiment 2
[0045] The difference from Example 1 is that when selecting the backfill layer of gravel-grained soil, due to the small deformation of gravel-grained soil, the gap-type arrangement of operating points in step A2 is 30cm apart from the edge of each operating point, and is arranged in an equilateral triangle. , The distance between the working point near the back of the platform and the back of the platform is 50cm; in step B1, repeat 5 sets, in step B2, when the relative settlement difference between the 5th and 4th sets is less than 10mm, stop the point The measured compaction coefficient within a depth of 1m below the construction surface is 0.94, and the K30 value is 134Mpa / m.
Embodiment 3
[0047] Such as figure 2 As shown, on the basis of embodiment 1, the following improvements are made: the ram plate includes a first ram plate 10 and a second ram plate 20, the first ram plate 10 is a truncated cone-shaped structure, and the middle of the first ram plate 10 is provided with The stepped hole 12, the buffer pad 11 on the stepped surface of the stepped hole 12, the cross section of the second ram plate 20 is T-shaped, the second ram plate 20 is sleeved in the stepped hole 12, the top surface of the second ram plate 20 and the ram 30 The thickness of the fixedly connected second ram plate 20 is equal to the sum of the thickness of the first ram plate 10 and the amount of deformation of the cushion 11. When the rammer strikes, the second ram plate 20 first moves downwards, and the second ram plate 20 then transmits the force to the first ram plate 10 through the cushion 11, and the first ram plate 10 undergoes a deformation process in the cushion 11 The force recei...
PUM
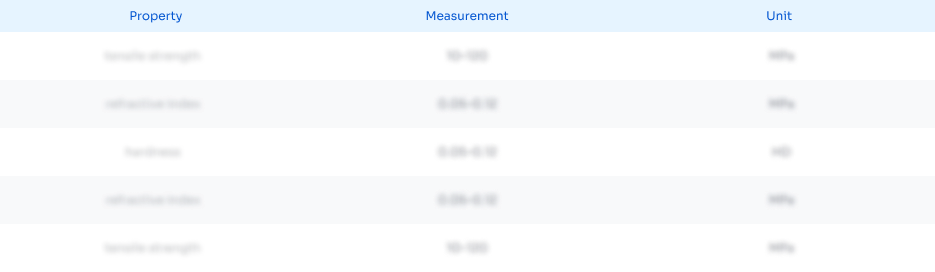
Abstract
Description
Claims
Application Information

- R&D
- Intellectual Property
- Life Sciences
- Materials
- Tech Scout
- Unparalleled Data Quality
- Higher Quality Content
- 60% Fewer Hallucinations
Browse by: Latest US Patents, China's latest patents, Technical Efficacy Thesaurus, Application Domain, Technology Topic, Popular Technical Reports.
© 2025 PatSnap. All rights reserved.Legal|Privacy policy|Modern Slavery Act Transparency Statement|Sitemap|About US| Contact US: help@patsnap.com