Raw material recovery technology in sulfur tetrafluoride production
A technology of sulfur tetrafluoride and raw materials, which is applied in the field of raw material recovery technology in the production of sulfur tetrafluoride, can solve problems such as low recovery rate, low fluorine utilization rate, and high impurity content, so as to achieve pure recovery of raw materials and increase recovery rate , Improve the effect of purification
- Summary
- Abstract
- Description
- Claims
- Application Information
AI Technical Summary
Problems solved by technology
Method used
Examples
Embodiment 1
[0038] A raw material recovery process in the production of sulfur tetrafluoride, comprising the following steps:
[0039] 1) Protective measures before the preparation of sulfur tetrafluoride:
[0040] Wear gas masks, safety glasses, cloth gas suits and chemical-resistant gloves;
[0041] 2) Preparation of sulfur tetrafluoride:
[0042] Prepare the instruments and materials for the production of sulfur tetrafluoride;
[0043] 3) Pre-preparation of sulfur tetrafluoride:
[0044] 425 g (11 moles) of finely divided sodium fluoride and 1 liter of dry acetonitrile were placed in a flask, and 525 g (3330 ml, 6 moles) of distilled sulfur dichloride (boiling point at 130 mm (20-25°C) was added dropwise to the stirring slurry with an initial temperature of 25°C within half an hour, and the temperature rose to about 42°C automatically during the dropping process. A small amount of product can be collected in the container;
[0045] 4) Preparation of sulfur tetrafluoride:
[0046]...
Embodiment 2
[0062] A raw material recovery process in the production of sulfur tetrafluoride, comprising the following steps:
[0063] 1) Protective measures before the preparation of sulfur tetrafluoride:
[0064] Wear gas masks, safety glasses, cloth gas suits and chemical-resistant gloves;
[0065] 2) Preparation of sulfur tetrafluoride:
[0066] Prepare the instruments and materials for the production of sulfur tetrafluoride;
[0067] 3) Pre-preparation of sulfur tetrafluoride:
[0068] 425 g (11 moles) of finely divided sodium fluoride and 1 liter of dry acetonitrile were placed in a flask, and 525 g (3330 ml, 6 moles) of distilled sulfur dichloride (boiling point at 130 mm (20-25°C) was added dropwise to the stirring slurry with an initial temperature of 25°C within half an hour, and the temperature rose to about 42°C automatically during the dropping process. A small amount of product can be collected in the container;
[0069] 4) Preparation of sulfur tetrafluoride:
[0070]...
Embodiment 3
[0086] A raw material recovery process in the production of sulfur tetrafluoride, comprising the following steps:
[0087] 1) Protective measures before the preparation of sulfur tetrafluoride:
[0088] Wear gas masks, safety glasses, cloth gas suits and chemical-resistant gloves;
[0089] 2) Preparation of sulfur tetrafluoride:
[0090] Prepare the instruments and materials for the production of sulfur tetrafluoride;
[0091] 3) Pre-preparation of sulfur tetrafluoride:
[0092] 425 g (11 moles) of finely divided sodium fluoride and 1 liter of dry acetonitrile were placed in a flask, and 525 g (3330 ml, 6 moles) of distilled sulfur dichloride (boiling point at 130 mm (20-25°C) was added dropwise to the stirring slurry with an initial temperature of 25°C within half an hour, and the temperature rose to about 42°C automatically during the dropping process. A small amount of product can be collected in the container;
[0093] 4) Preparation of sulfur tetrafluoride:
[0094]...
PUM
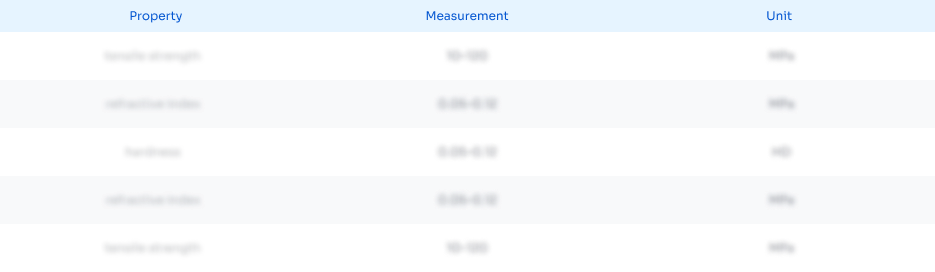
Abstract
Description
Claims
Application Information

- R&D Engineer
- R&D Manager
- IP Professional
- Industry Leading Data Capabilities
- Powerful AI technology
- Patent DNA Extraction
Browse by: Latest US Patents, China's latest patents, Technical Efficacy Thesaurus, Application Domain, Technology Topic, Popular Technical Reports.
© 2024 PatSnap. All rights reserved.Legal|Privacy policy|Modern Slavery Act Transparency Statement|Sitemap|About US| Contact US: help@patsnap.com