Multi-coordinate system collaborative 3D printer
A 3D printer and multi-coordinate system technology, applied in the field of 3D printing, can solve problems such as the inability to achieve multi-coordinate system collaborative printing, and achieve the effects of wide application range, improved printing accuracy, and guaranteed reliability.
- Summary
- Abstract
- Description
- Claims
- Application Information
AI Technical Summary
Problems solved by technology
Method used
Image
Examples
specific Embodiment approach
[0020] A specific embodiment of a multi-coordinate system collaborative 3D printer of the present invention is:
[0021] When printing an ordinary plane combination (no arc), the algorithm of ordinary Cartesian 3D printing is used. The six-axis mechanical arm 1 does not work, the electromagnetic chassis 3 is placed on the tray frame 11, and the electromagnetic chassis 3 remains horizontal. The nozzle mechanism prints the product according to the predetermined procedure.
[0022] When printing a plane arc combination, on the basis of the original Cartesian coordinate system, the six-axis robotic arm 1 plays a role. When printing a normal structure (no arc), the six-axis robotic arm 1 remains stationary, and the electromagnet does not move. When energized, the permanent magnet is adsorbed to the iron disc 10 fixedly connected to the motor to keep still. When printing the arc part of the assembly, the system retains the relative position memory of the nozzle 9 and the heating b...
PUM
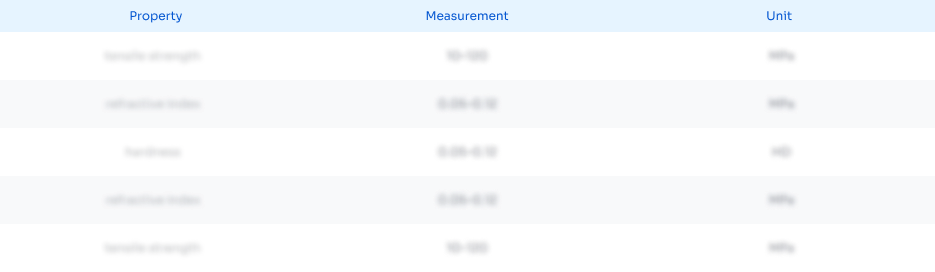
Abstract
Description
Claims
Application Information

- R&D
- Intellectual Property
- Life Sciences
- Materials
- Tech Scout
- Unparalleled Data Quality
- Higher Quality Content
- 60% Fewer Hallucinations
Browse by: Latest US Patents, China's latest patents, Technical Efficacy Thesaurus, Application Domain, Technology Topic, Popular Technical Reports.
© 2025 PatSnap. All rights reserved.Legal|Privacy policy|Modern Slavery Act Transparency Statement|Sitemap|About US| Contact US: help@patsnap.com