Visual servo laser positioning system and method of picking robot
A picking robot and visual servo technology, which is applied in the field of visual servo laser positioning system, can solve the problems of low scanning resolution, difficulty in accurately obtaining the spatial position of objects, and inability to obtain accurate information of objects, so as to reduce costs, improve measurement accuracy, The effect of reducing the amount of data processing
- Summary
- Abstract
- Description
- Claims
- Application Information
AI Technical Summary
Problems solved by technology
Method used
Image
Examples
Embodiment 1
[0054] like figure 1 As shown, Embodiment 1 of the present invention provides a visual servo laser positioning system for a picking robot. After the system positions the picked objects, it needs to cooperate with an external grabbing device for picking operations. The positioning system specifically includes a controller (not shown in the figure, a single-chip microcomputer can be used, or a computer can be directly used to run the control software), a monocular camera 1, and a laser ranging module 2 arranged below the monocular camera 1. 1 and the laser ranging module 2 are connected to the controller by communication; the laser ranging module 2 is installed on the two-dimensional pan-tilt 3, and the two-dimensional pan-tilt 3 includes an X-axis servo motor 4 that controls the horizontal rotation of the laser ranging module 2, and Control the Y-axis servo motor 5 that the laser ranging module 2 rotates vertically;
[0055] The controller adjusts and trains the existing deep ...
Embodiment 2
[0059] like figure 2 As shown, present embodiment 2 provides a kind of visual servo laser positioning system of picking robot on the basis of embodiment 1, and this embodiment 2 further defines that the controller includes the following parts:
[0060] The training module 6 is used to carry out training, verification and testing as a sample set with a plurality of sample images taken by the monocular camera 1 in the picking environment, to obtain a well-trained deep learning network algorithm;
[0061] The training method can use saturation, edge features, feature classification and other methods to learn and train the sample images in order to accurately identify the target object from the picking environment;
[0062] The image positioning module 7 is used to locate the target object in the two-dimensional image of the picking environment obtained by the monocular camera 1, and obtain the spatial position coordinates of the target object relative to the monocular camera 1, ...
Embodiment 3
[0068] like image 3 As shown, the present embodiment 3 provides the visual servo laser positioning method of the picking robot applying the above-mentioned system, which specifically includes the following steps:
[0069] S1: Adjust and train existing deep learning network algorithms;
[0070] S2: Obtain the two-dimensional image of the picking environment through the monocular camera 1, input it into the trained deep learning network algorithm to identify the target object, and output the image pixel coordinates of multiple target objects; convert the coordinates of the target object into the target object relative The direction and angle information of the monocular camera 1;
[0071] S3: control the angle at which the two-dimensional pan-tilt 3 points to the direction of the object to be measured, and perform distance measurement by the laser ranging module 2; calculate the actual spatial information of the object to be measured according to the measured distance and angl...
PUM
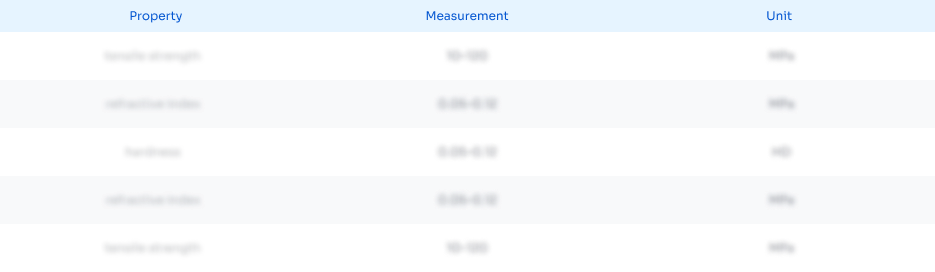
Abstract
Description
Claims
Application Information

- R&D Engineer
- R&D Manager
- IP Professional
- Industry Leading Data Capabilities
- Powerful AI technology
- Patent DNA Extraction
Browse by: Latest US Patents, China's latest patents, Technical Efficacy Thesaurus, Application Domain, Technology Topic, Popular Technical Reports.
© 2024 PatSnap. All rights reserved.Legal|Privacy policy|Modern Slavery Act Transparency Statement|Sitemap|About US| Contact US: help@patsnap.com