Pipeline welding seam milling robot
A robot and pipeline technology, applied in the field of robots, can solve the problems of high labor cost, low cleaning efficiency, unsatisfactory, etc., and achieve the effect of high cutting and milling efficiency, good cutting and milling quality, and convenient operation
- Summary
- Abstract
- Description
- Claims
- Application Information
AI Technical Summary
Problems solved by technology
Method used
Image
Examples
Embodiment Construction
[0025] figure 1 It is a schematic diagram of the three-dimensional structure of the present invention; figure 2 It is a schematic diagram of the structure of the clutch assembly; image 3 It is a schematic diagram of a partial three-dimensional structure of the present invention; Figure 4 It is a schematic diagram of the plane structure of the present invention; Figure 5 for Figure 4 Schematic diagram of side view structure;
[0026] In this embodiment, the left and right direction is the axial direction after the robot is matched with the pipeline; the axial direction of the robot is consistent with the axial direction of the pipeline after the robot is matched with the pipeline, and the radial direction of the robot is the radial direction of the pipeline after the robot is matched with the pipeline. same direction;
[0027] This embodiment provides a pipeline weld seam cutting and milling robot, which includes a vehicle frame, a walking device installed on the vehi...
PUM
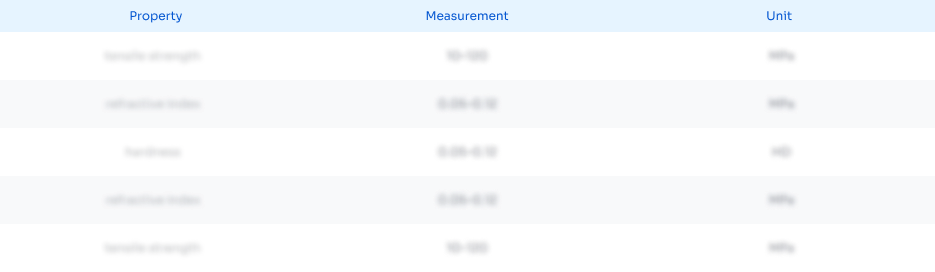
Abstract
Description
Claims
Application Information

- R&D
- Intellectual Property
- Life Sciences
- Materials
- Tech Scout
- Unparalleled Data Quality
- Higher Quality Content
- 60% Fewer Hallucinations
Browse by: Latest US Patents, China's latest patents, Technical Efficacy Thesaurus, Application Domain, Technology Topic, Popular Technical Reports.
© 2025 PatSnap. All rights reserved.Legal|Privacy policy|Modern Slavery Act Transparency Statement|Sitemap|About US| Contact US: help@patsnap.com