Method for Obtaining Modulus of Elasticity of Plate Members
A technology of plate-shaped components and elastic modulus, which is applied in the field of obtaining the elastic modulus of plate-shaped components, and can solve the problems of poor accuracy of the elastic modulus of plate-shaped components
- Summary
- Abstract
- Description
- Claims
- Application Information
AI Technical Summary
Problems solved by technology
Method used
Image
Examples
Embodiment Construction
[0056] In order to enable those skilled in the art to better understand the technical solutions of the present invention, the present invention will be described in detail below in conjunction with the accompanying drawings and specific embodiments.
[0057] The embodiment of the present invention discloses a method for obtaining the modulus of elasticity of the plate member 10, comprising the following steps:
[0058] S10: Establish three-point stress test conditions to obtain the pressure P on the plate member 10 and the deflection Umax generated based on the pressure P;
[0059] S20: Obtain the relational expressions about the elastic modulus E, the pressure P and the deflection Umax of the plate member 10 based on the plate and shell theory;
[0060] S30: Calculate the elastic modulus E of the plate-shaped member 10 based on the pressure P and the deflection Umax.
[0061] Preferably, as figure 1 , S10 includes the following steps:
[0062] S11: two support bars are arr...
PUM
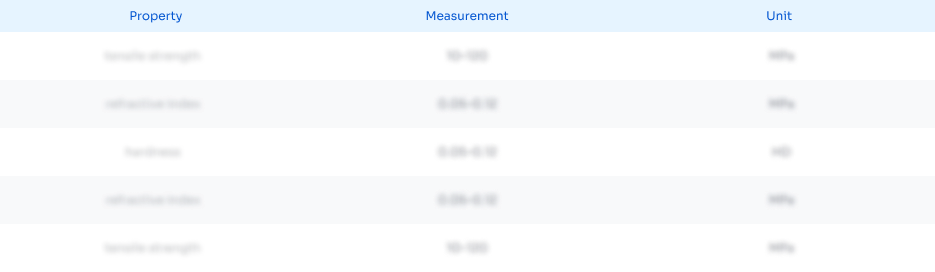
Abstract
Description
Claims
Application Information

- R&D
- Intellectual Property
- Life Sciences
- Materials
- Tech Scout
- Unparalleled Data Quality
- Higher Quality Content
- 60% Fewer Hallucinations
Browse by: Latest US Patents, China's latest patents, Technical Efficacy Thesaurus, Application Domain, Technology Topic, Popular Technical Reports.
© 2025 PatSnap. All rights reserved.Legal|Privacy policy|Modern Slavery Act Transparency Statement|Sitemap|About US| Contact US: help@patsnap.com