Mouse cage elastic support bearing cavity structure
A technology of elastic support and bearing cavity, which is applied in the direction of jet propulsion devices, engine components, rocket engine devices, etc., can solve the problems that cannot meet the use requirements of combined power engines, and achieve the goal of improving engine efficiency, compact structure size, and ensuring normal operation Effect
- Summary
- Abstract
- Description
- Claims
- Application Information
AI Technical Summary
Problems solved by technology
Method used
Image
Examples
Embodiment Construction
[0034] The invention discloses a squirrel cage elastic support bearing cavity structure, which is a brand-new scheme for the structural design of the combined power engine bearing cavity. A squirrel cage elastic support bearing cavity structure provided by the present invention combines Figure 1-2 , including a housing 1, an oil inlet pipe 2 arranged on the housing 1, a turn-back type squirrel cage elastic support 3 arranged in the housing, a contact end face seal assembly 4, a grate tooth for lubricating oil seal 5, a graphite ring 6, and a bearing 7, snap ring 8, O-shaped rubber sealing ring 9 and rotating shaft etc.
[0035] The housing 1 is provided with an annular groove composed of an inner ring and an outer ring, and the inner ring is provided with a plurality of small holes evenly distributed around the circumference, combined with Figure 4 , the small holes are evenly distributed along the circumference of the end face; the foldback type squirrel cage elastic suppo...
PUM
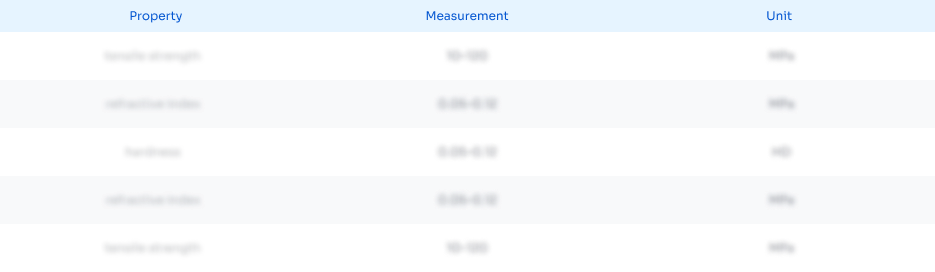
Abstract
Description
Claims
Application Information

- Generate Ideas
- Intellectual Property
- Life Sciences
- Materials
- Tech Scout
- Unparalleled Data Quality
- Higher Quality Content
- 60% Fewer Hallucinations
Browse by: Latest US Patents, China's latest patents, Technical Efficacy Thesaurus, Application Domain, Technology Topic, Popular Technical Reports.
© 2025 PatSnap. All rights reserved.Legal|Privacy policy|Modern Slavery Act Transparency Statement|Sitemap|About US| Contact US: help@patsnap.com