a combing method
A combing and fiber technology, applied in the field of spinning, can solve the problems of fiber damage, time-consuming and labor-intensive, etc., and achieve the effect of reducing fiber breakage, reducing short-lint rate, and avoiding fiber damage
- Summary
- Abstract
- Description
- Claims
- Application Information
AI Technical Summary
Problems solved by technology
Method used
Image
Examples
Embodiment 1
[0057] A combing method, the average fiber length in the combed cotton layer is 26mm, and the distribution histogram is as follows Figure 5 , the average fiber fineness is 0.17tex, and the histogram of fineness distribution is as follows Figure 6 , the average straightness of the fibers is 0.7, the number of fibers in the cross-section of the cotton layer is 1000, the process parameters are: the working angle of the tooth piece is 48°, the tooth density of the top comb is 150 teeth / 100mm, the tooth tip angle is 18°, the cylinder tooth surface The central angle is 60°, the total number of teeth in the cylinder is 15,000 teeth, and the average tooth density of the cylinder is 22 teeth / cm 2 , the cotton feeding length is 5.2mm, the noil distance is 10mm, and the dead zone length is 7.8mm.
[0058] After combing, the number of neps in the yarn of the cotton layer is reduced by 65% compared with that before combing, the short-lint rate of the combed sliver is 7.5%, the proport...
Embodiment 2
[0066] A kind of combing method, the average length of the fiber in the combed cotton layer is 29mm, the average fiber fineness is 0.16tex, the average straightness of the fiber is 0.72, the process parameters are: the working angle of the teeth is 50 °, the top comb The tooth density is 180 teeth / 100mm, the tooth tip angle is 19°, the central angle of the cylinder tooth surface is 62°, the total number of teeth in the cylinder is 15600 teeth, and the average tooth density of the cylinder is 26 teeth / cm 2 , the cotton feeding length is 4mm, the noil distance is 8mm, and the dead zone length is 8.12mm. After combing, the number of neps in the yarn of the cotton layer decreased by 68% compared with that before combing, the short-lint rate of the combed sliver was 7.6%, and the proportion of broken fibers was 3%.
Embodiment 3
[0068] A kind of combing method, the average length of the fiber in the combed cotton layer is 32mm, the average fiber fineness is 0.167tex, the average straightness of the fiber is 0.74, the process parameters are: the working angle of the teeth is 55 °, the top comb The tooth density is 200 teeth / 100mm, the tooth tip angle is 20°, the central angle of the cylinder tooth surface is 68°, the total number of teeth in the cylinder is 16000 teeth, and the average tooth density of the cylinder is 29 teeth / cm 2 , the cotton feeding length is 4.8mm, the noil distance is 9mm, and the dead zone length is 8.32mm. After combing, the number of neps in the yarn of the cotton layer decreased by 64% compared with that before combing, the short-lint rate of the combed sliver was 7.4%, and the proportion of broken fibers was 3.5%.
PUM
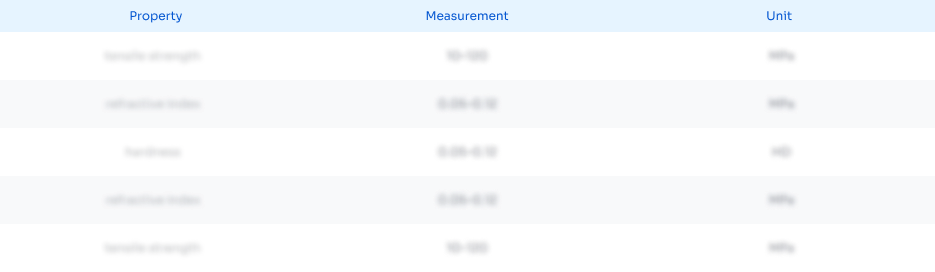
Abstract
Description
Claims
Application Information

- R&D
- Intellectual Property
- Life Sciences
- Materials
- Tech Scout
- Unparalleled Data Quality
- Higher Quality Content
- 60% Fewer Hallucinations
Browse by: Latest US Patents, China's latest patents, Technical Efficacy Thesaurus, Application Domain, Technology Topic, Popular Technical Reports.
© 2025 PatSnap. All rights reserved.Legal|Privacy policy|Modern Slavery Act Transparency Statement|Sitemap|About US| Contact US: help@patsnap.com