Intelligent material-based active vibration isolation base system capable of controlling bearing force transmission
A technology of intelligent materials and bearing bases, which is applied to the rigid brackets of bearing components, bearing components, shafts and bearings, etc., can solve the problems of inability to transmit dynamic force of bearings, large hull structure size, and complex comprehensive evaluation methods. Save installation space, high compatibility, small actuation displacement
- Summary
- Abstract
- Description
- Claims
- Application Information
AI Technical Summary
Problems solved by technology
Method used
Image
Examples
Embodiment Construction
[0020] The specific embodiments of the present invention will be further described below in conjunction with the accompanying drawings.
[0021] In view of the deficiencies in the prior art, the purpose of the present invention is to provide a bearing active vibration isolation base system, which can reduce the underwater low-frequency line spectrum radiation noise of the ship caused by the whirling vibration of the propulsion shafting by controlling the bearing force transmission. The intelligent material structure with the characteristics of large static stiffness, large actuating force and small actuating displacement is used as an active control actuator to meet the existing requirements of shafting alignment and bearing installation, and at the same time, the shafting supports the bearing through the radial direction The direct transmission of vibration force from its bearing base to the hull is used as a feedback signal for active control to control its vibration transmis...
PUM
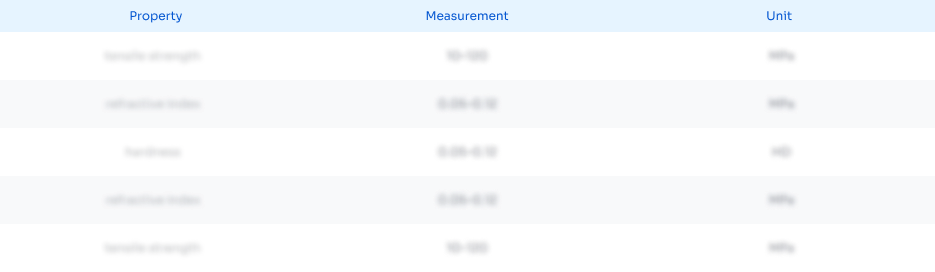
Abstract
Description
Claims
Application Information

- R&D
- Intellectual Property
- Life Sciences
- Materials
- Tech Scout
- Unparalleled Data Quality
- Higher Quality Content
- 60% Fewer Hallucinations
Browse by: Latest US Patents, China's latest patents, Technical Efficacy Thesaurus, Application Domain, Technology Topic, Popular Technical Reports.
© 2025 PatSnap. All rights reserved.Legal|Privacy policy|Modern Slavery Act Transparency Statement|Sitemap|About US| Contact US: help@patsnap.com