Copolymer rubber and method for producing same, and crosslinked rubber composition
A manufacturing method and technology for copolymers, applied in the field of cross-linked rubber products, can solve problems such as high reactivity and gelation, and achieve the effects of excellent dispersibility and excellent wear resistance
- Summary
- Abstract
- Description
- Claims
- Application Information
AI Technical Summary
Problems solved by technology
Method used
Image
Examples
Embodiment
[0113] Hereinafter, although an Example demonstrates this invention concretely, this invention is not limited to these Examples. In addition, the part in each example is a weight part unless otherwise indicated, and the evaluation of each physical property was performed by the method shown below.
[0114] 1) Molecular weight and molecular weight distribution
[0115] Molecular weight and molecular weight distribution were measured using GPC (manufactured by Tosoh, HLC-8220GPC), using tetrahydrofuran (Tetrahydrofuran, THF) in the solvent, and using a monodisperse polymer at a flow rate of 1.0 ml / min and a column temperature of 38°C. A calibration curve for styrene was used.
[0116] 2) Structure of polyfunctional vinyl aromatic copolymer
[0117] Using the JNM-LA600 nuclear magnetic resonance spectrometer manufactured by JEOL, through 13 C-nuclearmagnetic resonance (NMR) and 1 H-NMR analysis to determine. As a vehicle, use chloroform-d 1 , and the resonance line of tetram...
Synthetic example 1
[0129] 320.5 mL of DVB-810 (manufactured by Nippon Steel & Sumikin Chemicals, with a divinylbenzene content of 81.0% by weight) (1.82 moles of divinylbenzene and 0.43 moles of ethylvinylbenzene), n-butyl acetate 0.28 moles (36.9 mL) and 140 mL of toluene were put into a 1.0 L reactor, and a solution in which 40 millimoles of methanesulfonic acid was dissolved in 0.12 moles (15.7 mL) of n-butyl acetate was added at 70°C to react 6 Hour. After stopping the polymerization solution with calcium hydroxide, it filtered using activated alumina as a filter aid. Thereafter, 22.6 g of a soluble polyfunctional vinyl aromatic copolymer (copolymer X1) was obtained by devolatilization under reduced pressure at 60°C.
[0130] Mn of the obtained copolymer X1 was 1085, Mw was 12400, and Mw / Mn was 11.4. Through GC analysis, GPC measurement, FT-IR, 13 C-NMR and 1 H-NMR analysis confirmed that the copolymer X has the following vinyl group-containing structural unit (a1) and terminal group (d1...
Synthetic example 2
[0139] Put 276.4 mL of DVB-810, 86.2 mL of toluene, and 93.74 mL of anisole into a 1.0 L reactor, add a solution of 10 mmol of methanesulfonic acid dissolved in 2 mL of toluene at 50°C, and react for 4 hours , except that, the copolymer X2 was obtained by the same method as in Synthesis Example 1.
[0140] Mn of the obtained copolymer X2 was 1000, Mw was 18800, and Mw / Mn was 18.8. Through GC analysis, GPC measurement, FT-IR, 13 C-NMR and 1 H-NMR analysis confirmed that the copolymer X2 has the same vinyl group-containing structural unit (a1) derived from the divinyl aromatic compound (a) as in Synthesis Example 1, and the following Terminal group (d3).
[0141] [chemical 9]
[0142]
[0143] (* is the bonding part with the main chain of the copolymer)
[0144] Copolymer X2 contained 64.0 mol % of structural units (a) derived from divinylbenzene components with respect to all structures, and contained 2.0 terminal structural groups (d3) derived from anisole per molecule...
PUM
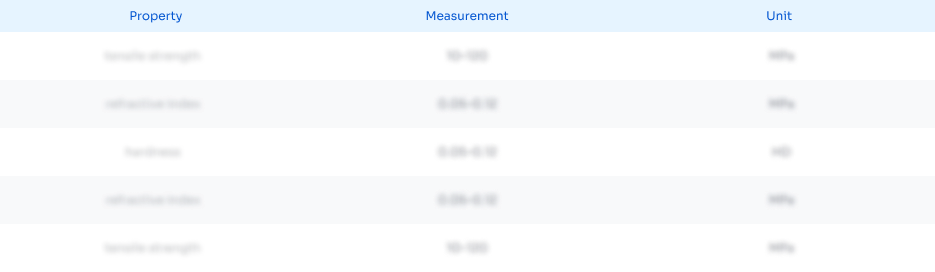
Abstract
Description
Claims
Application Information

- R&D
- Intellectual Property
- Life Sciences
- Materials
- Tech Scout
- Unparalleled Data Quality
- Higher Quality Content
- 60% Fewer Hallucinations
Browse by: Latest US Patents, China's latest patents, Technical Efficacy Thesaurus, Application Domain, Technology Topic, Popular Technical Reports.
© 2025 PatSnap. All rights reserved.Legal|Privacy policy|Modern Slavery Act Transparency Statement|Sitemap|About US| Contact US: help@patsnap.com