Tank type online defoaming machine and defoaming process thereof
A defoaming machine and defoaming technology, applied in nonlinear optics, instruments, optics, etc., can solve problems such as restricting the increase in production capacity of the entire line, position shift of glass sheets, long production line stagnation time, etc., and improve heat exchange efficiency. , Speed up the air pressure lifting speed, and solve the effect of the displacement of the glass sheet
- Summary
- Abstract
- Description
- Claims
- Application Information
AI Technical Summary
Problems solved by technology
Method used
Image
Examples
Embodiment Construction
[0038] The present invention will be further described below in conjunction with accompanying drawing:
[0039] Such as Figure 1 to Figure 13 As shown, the technical scheme adopted by the present invention is as follows: a tank-type online defoaming machine, comprising a feeding manipulator 2, a material picking and discharging manipulator 3, a defoaming tank 4, a feeding mechanism 5 and a feeding manipulator 6, wherein the above-mentioned The defoaming tank 4 includes two, and the two defoaming tanks 4 are arranged side by side on the machine platform 1 at intervals; the above-mentioned pick-and-discharge manipulator 3 is straddled above the two defoaming tanks 4 along the straight line; the above-mentioned fetching mechanism 5 includes two sets, The two fetching and sending mechanisms 5 are respectively arranged on the front side of the degassing tank 4; the above-mentioned feeding manipulator 2 is set on one side of the two degassing tanks 4, and the unloading manipulator ...
PUM
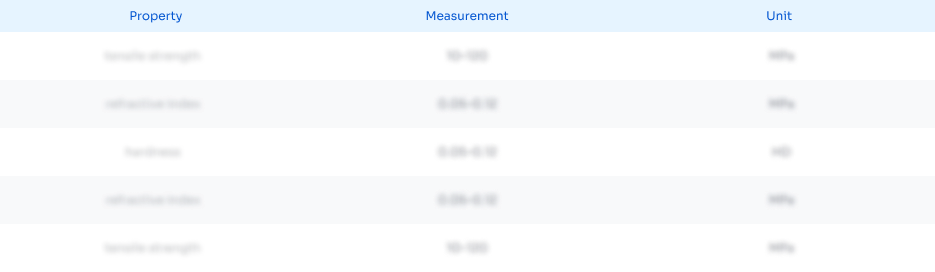
Abstract
Description
Claims
Application Information

- R&D
- Intellectual Property
- Life Sciences
- Materials
- Tech Scout
- Unparalleled Data Quality
- Higher Quality Content
- 60% Fewer Hallucinations
Browse by: Latest US Patents, China's latest patents, Technical Efficacy Thesaurus, Application Domain, Technology Topic, Popular Technical Reports.
© 2025 PatSnap. All rights reserved.Legal|Privacy policy|Modern Slavery Act Transparency Statement|Sitemap|About US| Contact US: help@patsnap.com