Preparation method of high-frequency high-impedance manganese zinc ferrite
A manganese-zinc ferrite, high-impedance technology, applied in the manufacture of inductors/transformers/magnets, electrical components, circuits, etc., can solve the problems of low impedance, low cut-off frequency, etc., to improve high-frequency performance and improve sintering Density and resistivity, loss reduction effect
- Summary
- Abstract
- Description
- Claims
- Application Information
AI Technical Summary
Problems solved by technology
Method used
Image
Examples
Embodiment 1
[0028] S1 ingredients, the following mass ratio ingredients: Fe 2 o 3 40wt%, MnO 30%, ZnO 25wt%, auxiliary materials 5wt%, auxiliary materials are dispersants and defoamers, and additives are also included. The additives include: SiO relative to the total weight of the main component 2 100ppm, CaCO 3 800ppm, Mo 3 O 500ppm, V 2 o 5 500ppm, CoO 100ppm;
[0029] S2 is dispersed, and the Fe in the above main components 2 o 3 , MnO, and ZnO material powders are wet-mixed evenly to obtain a slurry with a solid content of 50-70 wt %;
[0030] S3 sanding, the obtained slurry is sanded with pure water as a solvent;
[0031] S4 pressure filtration, dehydrating the sanded slurry to a moisture content of 10% to 20wt%;
[0032] S5 Extrusion granulation, the press-filtered powder is granulated by a twin-screw extruder, the diameter of the granulation is 1.5-12mm, and the length is 10-50mm;
[0033] S6 drying, drying the extruded granular raw material, the moisture content of th...
Embodiment 2
[0039] S1 ingredients, the following mass ratio ingredients: Fe 2 o 3 50wt%, MnO 30%, ZnO 15wt%, auxiliary materials 5wt%, auxiliary materials are dispersants and defoamers, and additives, additives include: SiO 2 120ppm, CaCO 3 860ppm, Mo 3 O 620ppm, V 2 o 5 530ppm, CoO 70ppm;
[0040] S2 is dispersed, and the Fe in the above main components 2 o 3 , MnO, and ZnO material powders are wet-mixed evenly to obtain a slurry with a solid content of 50-70 wt %;
[0041] S3 sanding, the obtained slurry is sanded with pure water as a solvent;
[0042] S4 pressure filtration, dehydrating the sanded slurry to a moisture content of 10% to 20wt%;
[0043] S5 Extrusion granulation, the press-filtered powder is granulated by a twin-screw extruder, the diameter of the granulation is 1.5-12mm, and the length is 10-50mm;
[0044] S6 drying, drying the extruded granular raw material, the moisture content of the material after drying is <3wt%;
[0045] The S7 rotary kiln is pre-fire...
Embodiment 3
[0050] S1 ingredients, the following mass ratio ingredients: Fe 2 o 3 55wt%, MnO 20%, ZnO 25wt%, auxiliary materials 5wt%, auxiliary materials are dispersants and defoamers, and additives, additives include: SiO 2 150ppm, CaCO 3 900ppm, Mo 3 O 700ppm, V 2 o 5 600ppm, CoO 150ppm;
[0051] S2 is dispersed, and the Fe in the above main components 2 o 3 , MnO, and ZnO material powders are wet-mixed evenly to obtain a slurry with a solid content of 50-70 wt %;
[0052] S3 sanding, the obtained slurry is sanded with pure water as a solvent;
[0053] S4 pressure filtration, dehydrating the sanded slurry to a moisture content of 10% to 20wt%;
[0054] S5 Extrusion granulation, the press-filtered powder is granulated by a twin-screw extruder, the diameter of the granulation is 1.5-12mm, and the length is 10-50mm;
[0055]S6 drying, drying the extruded granular raw material, the moisture content of the material after drying is <3wt%;
[0056] S7 rotary kiln pre-firing, the...
PUM
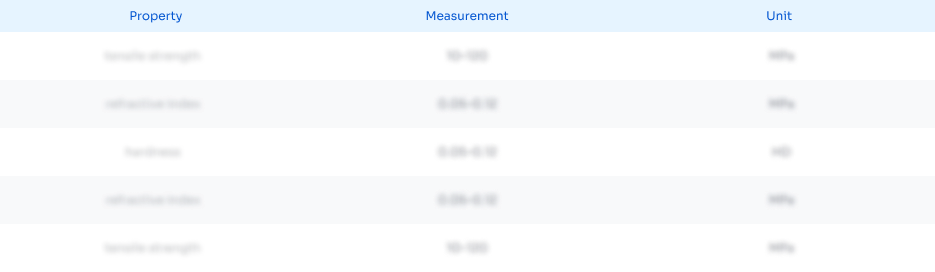
Abstract
Description
Claims
Application Information

- Generate Ideas
- Intellectual Property
- Life Sciences
- Materials
- Tech Scout
- Unparalleled Data Quality
- Higher Quality Content
- 60% Fewer Hallucinations
Browse by: Latest US Patents, China's latest patents, Technical Efficacy Thesaurus, Application Domain, Technology Topic, Popular Technical Reports.
© 2025 PatSnap. All rights reserved.Legal|Privacy policy|Modern Slavery Act Transparency Statement|Sitemap|About US| Contact US: help@patsnap.com