Aluminum attachment method and vacuum conveying cavity structure of metallic thin film coating machine
A metal thin film, vacuum conveying technology, applied in metal material coating process, vacuum evaporation plating, coating and other directions, can solve the problems of increasing equipment manufacturing cost, spending a lot of time, low work efficiency, etc., to shorten the transportation distance, The effect of saving production costs and reducing production costs
- Summary
- Abstract
- Description
- Claims
- Application Information
AI Technical Summary
Problems solved by technology
Method used
Image
Examples
Embodiment Construction
[0042] see Figure 4 , Figure 5 As shown, the aluminum attachment method of the metal thin film coating machine according to the present invention is shown. Wherein, the metal thin film coating machine includes a vacuum transfer chamber 1 and a pre-etching reaction chamber 3 which is connected to the periphery of the vacuum transfer chamber 1 and is in a high vacuum state. arm 10. The aluminum attachment method includes:
[0043] (a) At least one placement rack 11 is provided at a position where the vacuum transfer chamber 1 does not affect the transfer of the wafer 8 by the robot arm 10, and the placement rack 11 can store an aluminum sheet 9;
[0044] (b) Utilize the mechanical arm 10 to remove the aluminum sheet 9 from the placement rack 11, and send it to the pre-etching reaction chamber 3;
[0045] (c) bombarding the aluminum sheet 9 with plasma in the pre-etching reaction chamber 3, so that the aluminum on the aluminum sheet 9 is plated on the inner wall of the pre-...
PUM
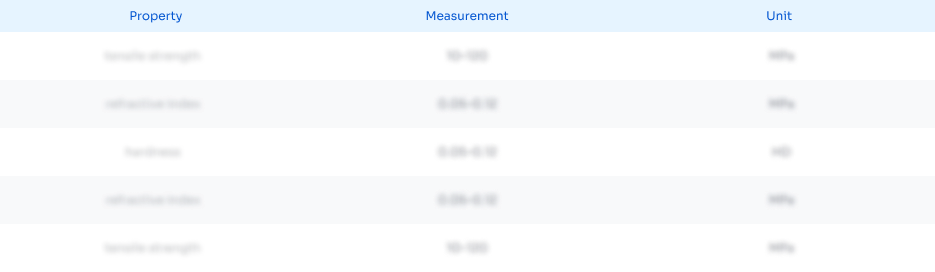
Abstract
Description
Claims
Application Information

- Generate Ideas
- Intellectual Property
- Life Sciences
- Materials
- Tech Scout
- Unparalleled Data Quality
- Higher Quality Content
- 60% Fewer Hallucinations
Browse by: Latest US Patents, China's latest patents, Technical Efficacy Thesaurus, Application Domain, Technology Topic, Popular Technical Reports.
© 2025 PatSnap. All rights reserved.Legal|Privacy policy|Modern Slavery Act Transparency Statement|Sitemap|About US| Contact US: help@patsnap.com