A Dynamic Balancing Method for Rotary Table of Double-axis Precision Centrifuge Based on Driving Current
A technology of precision centrifuge and driving current, applied in centrifuges and other directions, can solve the problems of time-consuming, low dynamic unbalance identification accuracy, complicated operation and calculation process, etc., achieve high sensitivity and identification accuracy, and improve dynamic balance accuracy. , the effect of shortening the dynamic balancing time
- Summary
- Abstract
- Description
- Claims
- Application Information
AI Technical Summary
Problems solved by technology
Method used
Image
Examples
specific Embodiment approach 1
[0040] Specific embodiment one: in conjunction with Fig. 1 (a), figure 2 and image 3 As shown, the implementation process of a method for dynamic balancing of a rotary table of a two-axis precision centrifuge based on driving current described in this embodiment is as follows:
[0041] Schematic diagram of the structure of the double-shaft arm precision centrifuge figure 2 As shown, the axis O of the rotary table of the double-axis arm precision centrifuge is defined as the origin of coordinates, the direction of the spindle center pointing to the axis of the rotary table on the same water surface as the axis of the rotary table is the positive direction of the x-axis, and the axis of the rotary table is upward The direction is the positive direction of the z-axis, and the direction of the y-axis is determined according to the right-hand rule; let the initial position of the static unbalanced particle be on the positive semi-axis of the x-axis, when the main shaft rotates at...
specific Embodiment approach 2
[0056] Specific embodiment two: the difference between this embodiment and specific embodiment one is that step three can also be implemented in the following manner, as shown in Figure 1(b):
[0057] Step 31. At the mechanical angular position φ of the turntable 1 Add a test weight of ξkg at -90°, collect the driving current data of the rotary table, extract the one-octave frequency component, and Do the difference to get the amplitude A of the double frequency of the current caused by the dynamic unbalance at this time m , m=2,3,...; Indicates that the driving current of the turntable before the mth counterweight is doubled;
[0058] Step 32. After each addition of trial weight, the amplitude A of the double frequency of the drive current of the turntable m Amplitude A of double frequency of the driving current of the turntable caused by dynamic unbalance when no trial weight is initially added 1 For comparison, when A m / A 1 When ≤20%, it is considered that the dyna...
Embodiment
[0060] Embodiment: The present invention is further described in detail in conjunction with accompanying drawings 1-7. A method for dynamic balancing of a rotary table of a two-axis precision centrifuge based on driving current described in the present invention can identify and balance dynamic unbalance in an ideal simulation It is carried out under the environment without adding friction and other undesirable factors, so there is no need to measure benchmark data.
PUM
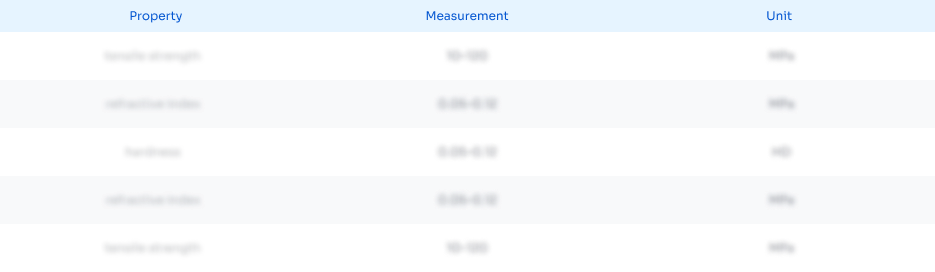
Abstract
Description
Claims
Application Information

- R&D
- Intellectual Property
- Life Sciences
- Materials
- Tech Scout
- Unparalleled Data Quality
- Higher Quality Content
- 60% Fewer Hallucinations
Browse by: Latest US Patents, China's latest patents, Technical Efficacy Thesaurus, Application Domain, Technology Topic, Popular Technical Reports.
© 2025 PatSnap. All rights reserved.Legal|Privacy policy|Modern Slavery Act Transparency Statement|Sitemap|About US| Contact US: help@patsnap.com