A kind of food-grade cellulose gum and preparation method thereof
A cellulose glue, food-grade technology, applied in the field of food-grade cellulose glue and its preparation, can solve the problem of fast viscosity reduction
- Summary
- Abstract
- Description
- Claims
- Application Information
AI Technical Summary
Problems solved by technology
Method used
Image
Examples
Embodiment 1
[0026] (1) Under stirring conditions, 1000g of the dissolving slurry with a degree of polymerization of 1920 is added to 940g of a mass concentration of 35% sodium hydroxide solution, and the temperature is controlled at 25-30°C for stirring and pretreatment for 80 minutes. The finished alkali cellulose is squeezed and filtered, and the treated alkali cellulose solid is left.
[0027] (2) the alkali cellulose that has been processed is 1708g, joins and puts 772g mass concentration and is that 52% sodium hydroxide aqueous solution and 2500g volume concentration are in the kneader of the mixed liquor of 92% alcohol aqueous solution, carry out stirring alkalization, temperature Control the temperature at 20-25°C, and control the alkalization time for 50 minutes.
[0028] (3) After the alkalization is finished, add 1000 g of chloroacetic acid alcohol solution with a mass concentration of 75%, and drop it in 15 minutes. The material is taken out.
[0029] (4) put the cooled mater...
Embodiment 2
[0033] (1) Under stirring conditions, 1000g of the dissolving slurry with a degree of polymerization of 2050 is added to 1095g of a mass concentration of 30% sodium hydroxide solution, and the temperature is controlled at 22-27°C for stirring and pretreatment for 50min. The finished alkali cellulose is squeezed and filtered, and the treated alkali cellulose solid is left.
[0034] (2) the alkali cellulose handled is 1750g, joins and puts 803g mass concentration and is that 50% sodium hydroxide aqueous solution and 2800g volume concentration are in the kneader of the mixed liquor of 94% alcohol aqueous solution, carry out stirring alkalization, temperature Control the temperature at 22-26°C, and control the alkalization time for 30 minutes.
[0035] (3) After the alkalization is finished, add 1000 g of chloroacetic acid alcohol solution with a mass concentration of 75%, and drop it in 30 minutes. The material is taken out.
[0036] (4) put the cooled material into the alcohol...
Embodiment 3
[0040] (1) Under stirring conditions, 1000g of the dissolving slurry with a degree of polymerization of 1810 is added to 1310g of a mass concentration of 25% sodium hydroxide solution, and the temperature is controlled at 15-20°C for agitation pretreatment for 120min, and the pretreatment The finished alkali cellulose is squeezed and filtered, and the treated alkali cellulose solid is left.
[0041] (2) the alkali cellulose that has been processed is 1800g, joins and puts 892g mass concentration and is that 45% sodium hydroxide aqueous solution and 3000g volume concentration are in the kneader of the mixed liquor of 93% alcohol aqueous solution, carry out stirring alkalization, temperature Control the temperature at 27-31°C, and control the alkalization time for 60 minutes.
[0042] (3) After the alkalization is finished, add 1000 g of chloroacetic acid alcohol solution with a mass concentration of 75%, and drop it in 20 minutes. The material is taken out.
[0043] (4) Put the...
PUM
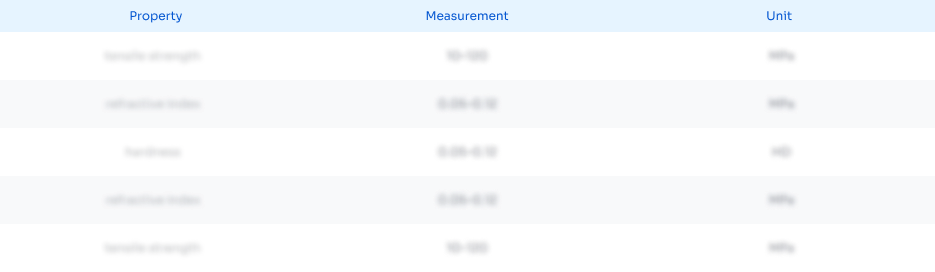
Abstract
Description
Claims
Application Information

- R&D
- Intellectual Property
- Life Sciences
- Materials
- Tech Scout
- Unparalleled Data Quality
- Higher Quality Content
- 60% Fewer Hallucinations
Browse by: Latest US Patents, China's latest patents, Technical Efficacy Thesaurus, Application Domain, Technology Topic, Popular Technical Reports.
© 2025 PatSnap. All rights reserved.Legal|Privacy policy|Modern Slavery Act Transparency Statement|Sitemap|About US| Contact US: help@patsnap.com