Aluminum coil pipe production method
A production method, the technology of aluminum coil, applied in the field of aluminum coil production, can solve the problems of affecting processing, difficulty in eliminating mechanical vibration of extrusion size tolerance, difference in overall performance of aluminum rods, etc., and achieve the effect of eliminating mechanical vibration
- Summary
- Abstract
- Description
- Claims
- Application Information
AI Technical Summary
Problems solved by technology
Method used
Examples
Embodiment Construction
[0020] Below in conjunction with embodiment the content of the present invention is described in further detail.
[0021] A method for producing an aluminum coil, comprising the steps of:
[0022] Aluminum rod melting and casting: inject aluminum water into the mold cavity to form aluminum rods, and use ceramic filter elements to filter and purify impurities. After the aluminum rods are formed, they are uniformly annealed. Carry out heat preservation treatment;
[0023] Thermal peeling: heat the aluminum rod after injection molding, pass the formed aluminum rod through the peeling machine, and use the scraper of the peeling machine to peel off the surface of the aluminum rod to remove the surface layer with more impurities and poor performance part;
[0024] Extrusion: put the aluminum rod into the isothermal extrusion die, which needs to be placed in the heating system, and under the state of isothermal, constant pressure and constant speed, the working belt of the twisting...
PUM
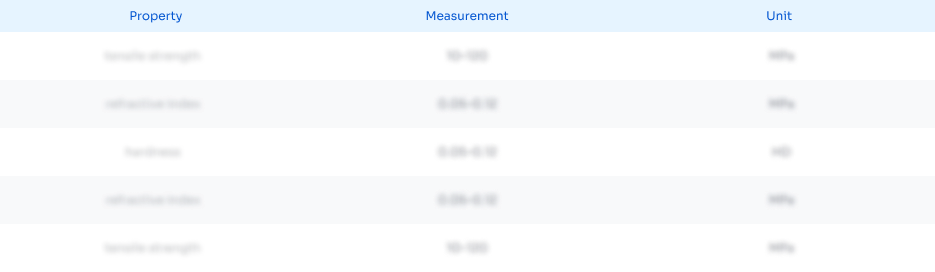
Abstract
Description
Claims
Application Information

- R&D
- Intellectual Property
- Life Sciences
- Materials
- Tech Scout
- Unparalleled Data Quality
- Higher Quality Content
- 60% Fewer Hallucinations
Browse by: Latest US Patents, China's latest patents, Technical Efficacy Thesaurus, Application Domain, Technology Topic, Popular Technical Reports.
© 2025 PatSnap. All rights reserved.Legal|Privacy policy|Modern Slavery Act Transparency Statement|Sitemap|About US| Contact US: help@patsnap.com