Pillar-type climbing robot
A technology for robots and steps, applied in the field of robots, can solve problems such as instability of robots on steps, and achieve the effect of restraining roll and enhancing matching accuracy.
- Summary
- Abstract
- Description
- Claims
- Application Information
AI Technical Summary
Problems solved by technology
Method used
Image
Examples
Embodiment Construction
[0031] The following will clearly and completely describe the technical solutions in the embodiments of the present invention with reference to the accompanying drawings in the embodiments of the present invention. Obviously, the described embodiments are only some, not all, embodiments of the present invention. Based on the embodiments of the present invention, all other embodiments obtained by persons of ordinary skill in the art without making creative efforts belong to the protection scope of the present invention.
[0032] Such as Figure 1 to Figure 3 As shown, the present invention provides a pillar-holding step-up robot, comprising a chassis frame 1, the upper end of the chassis frame 1 is connected with a lifting frame 2 which can move up and down; the lifting frame 2 is connected with a pillar-holding rotating mechanism 3. The column-holding rotation mechanism 3 can hold the column 4 on one side of the step 10 tightly and drive the chassis frame 1 to rotate around th...
PUM
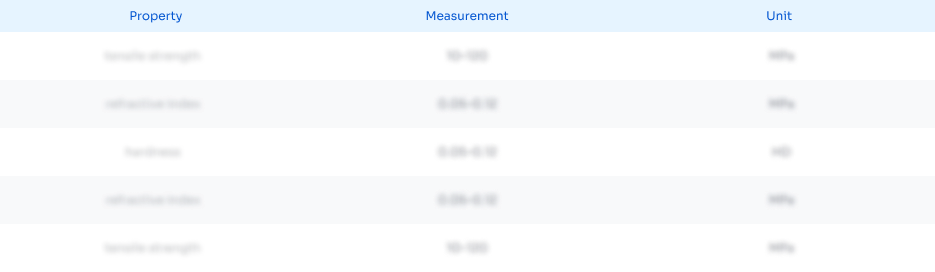
Abstract
Description
Claims
Application Information

- R&D
- Intellectual Property
- Life Sciences
- Materials
- Tech Scout
- Unparalleled Data Quality
- Higher Quality Content
- 60% Fewer Hallucinations
Browse by: Latest US Patents, China's latest patents, Technical Efficacy Thesaurus, Application Domain, Technology Topic, Popular Technical Reports.
© 2025 PatSnap. All rights reserved.Legal|Privacy policy|Modern Slavery Act Transparency Statement|Sitemap|About US| Contact US: help@patsnap.com