Internal mold fixing and external mold assembling type disassembly-free composite template and mounting method
A composite formwork and prefabricated technology, applied in building components, fire prevention, walls, etc., can solve the problems of formwork damage, serious pollution, labor and cost, etc., and achieve the effects of simple installation, good fire resistance, and improved efficiency.
- Summary
- Abstract
- Description
- Claims
- Application Information
AI Technical Summary
Problems solved by technology
Method used
Image
Examples
Embodiment Construction
[0027] Attached below figure 1 , 2 Taking the wooden formwork as an example, the inner mold fixing outer mold assembly type no-disassembly composite formwork and installation method of the present invention will be described in detail below.
[0028] as attached figure 1 , 2 As shown, the internal mold fixed external mold assembly type disassembly-free composite formwork of the present invention has a structure including an inner formwork 1, an insulation layer 2, a fireproof layer 3, a panel layer 4, an outer decorative layer 5, a secondary keel 6, and a main keel 7 and cable stays 8, the above-mentioned inner formwork 1 is a wooden formwork, the insulation layer 2 is made of polyurethane foam material, and the fireproof layer 3 is made of construction waste crushed materials containing bricks, stones, stone powder and fly ash, cement , water-retaining agent and additives are mixed according to the following proportions, construction waste crushed materials: 35-40%, fly as...
PUM
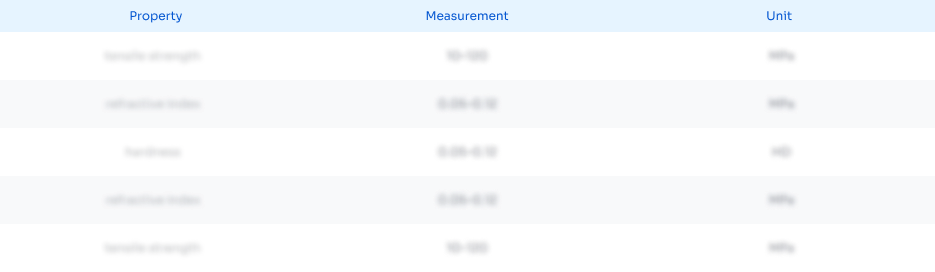
Abstract
Description
Claims
Application Information

- Generate Ideas
- Intellectual Property
- Life Sciences
- Materials
- Tech Scout
- Unparalleled Data Quality
- Higher Quality Content
- 60% Fewer Hallucinations
Browse by: Latest US Patents, China's latest patents, Technical Efficacy Thesaurus, Application Domain, Technology Topic, Popular Technical Reports.
© 2025 PatSnap. All rights reserved.Legal|Privacy policy|Modern Slavery Act Transparency Statement|Sitemap|About US| Contact US: help@patsnap.com