Machining Error Compensation Method of Thin-walled Parts Based on Mirror Image Method and Cubic Spline Interpolation
A technology of thin-walled parts processing and spline interpolation, which is applied in the direction of program control, instrument, computer control, etc., can solve the problems of ignoring the influence of processing deformation, complicated compensation process, and low compensation efficiency, so as to reduce the number of compensations and improve the compensation process. Simple, precision-enhancing effect
- Summary
- Abstract
- Description
- Claims
- Application Information
AI Technical Summary
Problems solved by technology
Method used
Image
Examples
Embodiment Construction
[0032] The present invention will be further described below in conjunction with the accompanying drawings and specific embodiments, but the following embodiments in no way limit the present invention.
[0033] Taking thin-walled aluminum alloy workpieces as an example, the process of error compensation processing for thin-walled parts using the mirror image method and cubic spline interpolation error compensation method is described in detail as follows:
[0034] Such as figure 1 As shown, the steps of the thin-walled part processing error compensation method are as follows:
[0035] S1. Process the initial blank to leave a certain margin of 3mm;
[0036] S2. Using the on-machine detection system, the machining error e of the workpiece surface is detected according to a certain sequence of sampling points on the workpiece surface after step S1 is completed. k ={e k1 、e k2 ,...,e kn}, and calculate the actual cutting depth value y of the corresponding sampling point seque...
PUM
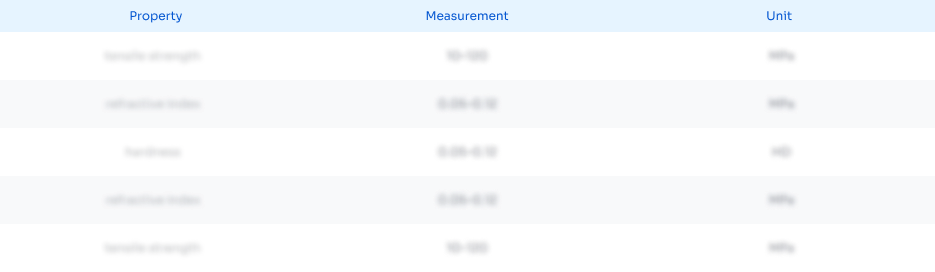
Abstract
Description
Claims
Application Information

- R&D
- Intellectual Property
- Life Sciences
- Materials
- Tech Scout
- Unparalleled Data Quality
- Higher Quality Content
- 60% Fewer Hallucinations
Browse by: Latest US Patents, China's latest patents, Technical Efficacy Thesaurus, Application Domain, Technology Topic, Popular Technical Reports.
© 2025 PatSnap. All rights reserved.Legal|Privacy policy|Modern Slavery Act Transparency Statement|Sitemap|About US| Contact US: help@patsnap.com