Foldable supporting arm hinged to automatic drive unit and driven by folding lead screw
An automatic drive and lead screw drive technology, applied in the aerospace field, can solve problems such as difficult antennas, limited deployment range, and small folding ratio, achieving the effects of wide application range, improving folding ratio, and saving launch costs
- Summary
- Abstract
- Description
- Claims
- Application Information
AI Technical Summary
Problems solved by technology
Method used
Image
Examples
specific Embodiment approach 1
[0031] Specific implementation mode one: combine figure 1 with figure 2 To illustrate this embodiment, an automatic hinge drive unit in this embodiment includes a motor 1, a first connecting body 2, a second connecting body 3, a lead screw 4, a nut 5, a guide rod 6 and a connecting rod 7;
[0032] The first connecting body 2 and the second connecting body 3 are hinged, and the first connecting body 2 is provided with a lead screw 4 and a guide rod 6, the axis of the lead screw 4 and the axis of the guide rod 6 are parallel to each other, and the lead screw 4 is driven by the motor 1 , the lead screw 4 is provided with a screw nut 5, the screw nut 5 is slidably arranged on the guide rod 6, one end of the connecting rod 7 is hinged with the screw nut 5, the other end of the connecting rod 7 is hinged with the second connecting body 3, and the connecting rod 7 The axis hinged with the second connecting body 3 and the axis hinged between the first connecting body 2 and the secon...
specific Embodiment approach 2
[0034] Specific implementation mode two: combination figure 1 with figure 2 To illustrate this embodiment, a manual drive device 8 is also provided between the lead screw 4 and the shaft of the motor 1 in this embodiment, and the manual drive device 8 includes a first bevel gear 8-1, a second bevel gear 8-2, a transmission shaft 8-3 and one-way rotation mechanism 8-4;
[0035] The transmission shaft 8-3 is fixed on the shaft of the motor 1, a one-way rotation mechanism 8-4 is arranged between the end of the transmission shaft 8-3 and the end of the lead screw 4, and the first bevel gear is fixed on the lead screw 4 8-1, the second bevel gear 8-2 is arranged on the first connecting body 2 through the rotating shaft, and the first bevel gear 8-1 and the second bevel gear 8-2 mesh with each other.
[0036] Other compositions and connections are the same as in the first embodiment.
specific Embodiment approach 3
[0037] Specific implementation mode three: combination figure 2 To illustrate this embodiment, the one-way rotation mechanism 8-4 of this embodiment includes a first compression spring 8-4-1 and two ratchet toothed sleeves 8-4-2;
[0038] One of the ratchet toothed sleeves 8-4-2 is slidably arranged on the transmission shaft 8-3 and can rotate together with the transmission shaft 8-3, and the first compression spring 8-4-1 is sleeved on the transmission shaft 8-3 and the two The ends are respectively supported on the first connecting body 2 and the end of one of the ratchet toothed sleeves 8-4-2, and the other ratchet toothed sleeve 8-4-2 is fixed on the end of the lead screw 4, The ratchet teeth on the two ratchet toothed sleeves 8-4-2 cooperate with each other under the action of the first compression spring 8-4-1.
[0039] The drive shaft 8-3 can be a spline shaft, or a square shaft, etc., which can generate torque to one of the ratchet toothed sleeves 8-4-2, and can make...
PUM
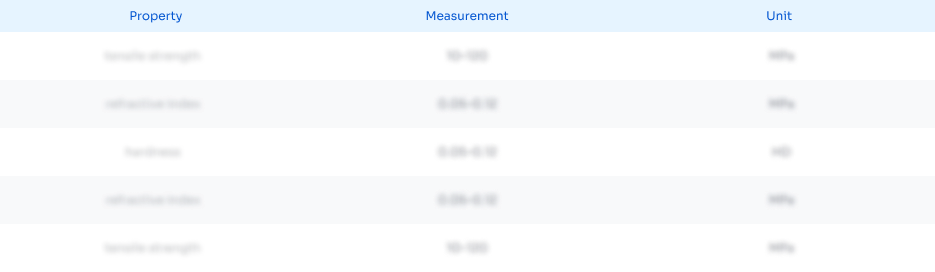
Abstract
Description
Claims
Application Information

- R&D Engineer
- R&D Manager
- IP Professional
- Industry Leading Data Capabilities
- Powerful AI technology
- Patent DNA Extraction
Browse by: Latest US Patents, China's latest patents, Technical Efficacy Thesaurus, Application Domain, Technology Topic, Popular Technical Reports.
© 2024 PatSnap. All rights reserved.Legal|Privacy policy|Modern Slavery Act Transparency Statement|Sitemap|About US| Contact US: help@patsnap.com