High-performance copper bus and preparation technology thereof
A preparation process and technology for copper busbars, which are applied in the field of high-performance copper busbars and their preparation processes, can solve the problems that copper busbars are susceptible to corrosion, affect power supply temperature and power supply safety, etc., and achieve corrosion resistance, good plasticity, and accurate shape. Size and appearance quality, simple and easy-to-control effects
- Summary
- Abstract
- Description
- Claims
- Application Information
AI Technical Summary
Problems solved by technology
Method used
Image
Examples
Embodiment 1
[0041] A high-performance copper busbar, its constituent elements include copper, titanium, silicon, ytterbium, zirconium, vanadium, niobium, strontium and inevitable impurities; the weight percentages of the constituent elements are as follows: copper 97.47%, titanium 1.2%, silicon 0.5% %, 0.1% of ytterbium, 0.5% of zirconium, 0.12% of vanadium, 0.06% of niobium, 0.02% of strontium, and 0.03% of unavoidable impurities in total.
[0042] A high-performance copper busbar preparation process, comprising the following steps:
[0043] S1: prepare materials, prepare raw materials of copper, titanium, silicon, ytterbium, zirconium, vanadium, niobium and strontium;
[0044] S2: smelting, the prepared raw materials, the raw materials of titanium, silicon, ytterbium, zirconium, vanadium, niobium, strontium are fully stirred and mixed and then added to a high-temperature smelting furnace for smelting;
[0045] Step S2 specifically includes the following steps:
[0046] S21: Preheating...
Embodiment 2
[0062] A high-performance copper busbar, its constituent elements include copper, titanium, silicon, ytterbium, zirconium, vanadium, niobium, strontium and inevitable impurities; the weight percentages of the constituent elements are as follows: copper 95.04%, titanium 2.6%, silicon 0.8% %, 0.3% of ytterbium, 0.9% of zirconium, 0.18% of vanadium, 0.1% of niobium, 0.05% of strontium and 0.03% of the total amount of inevitable impurities.
[0063] A high-performance copper busbar preparation process, comprising the following steps:
[0064] S1: prepare materials, prepare raw materials of copper, titanium, silicon, ytterbium, zirconium, vanadium, niobium and strontium;
[0065] S2: smelting, the prepared raw materials, the raw materials of titanium, silicon, ytterbium, zirconium, vanadium, niobium, strontium are fully stirred and mixed and then added to a high-temperature smelting furnace for smelting;
[0066] Step S2 also includes the following steps:
[0067] S21: Preheating...
Embodiment 3
[0083] A high-performance copper busbar, its constituent elements include copper, titanium, silicon, ytterbium, zirconium, vanadium, niobium, strontium and inevitable impurities; the weight percentages of the constituent elements are as follows: copper 96.21%, titanium 2%, silicon 0.6% %, 0.2% of ytterbium, 0.7% of zirconium, 0.15% of vanadium, 0.08% of niobium, 0.03% of strontium and 0.03% of unavoidable impurities in total.
[0084] A high-performance copper busbar preparation process, comprising the following steps:
[0085] S1: prepare materials, prepare raw materials of copper, titanium, silicon, ytterbium, zirconium, vanadium, niobium and strontium;
[0086] S2: smelting, the prepared raw materials, the raw materials of titanium, silicon, ytterbium, zirconium, vanadium, niobium, strontium are fully stirred and mixed and then added to a high-temperature smelting furnace for smelting;
[0087] Step S2 also includes the following steps:
[0088] S21: The furnace is prehea...
PUM
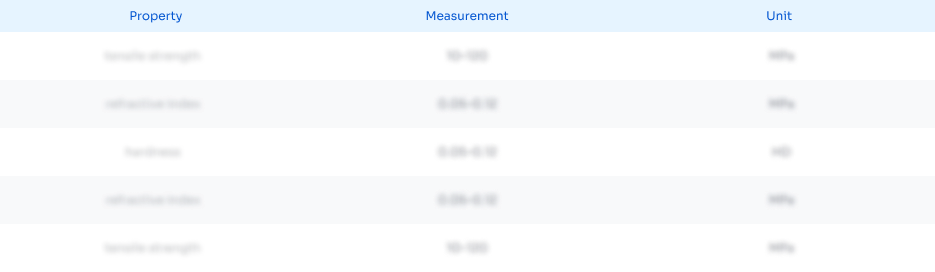
Abstract
Description
Claims
Application Information

- R&D
- Intellectual Property
- Life Sciences
- Materials
- Tech Scout
- Unparalleled Data Quality
- Higher Quality Content
- 60% Fewer Hallucinations
Browse by: Latest US Patents, China's latest patents, Technical Efficacy Thesaurus, Application Domain, Technology Topic, Popular Technical Reports.
© 2025 PatSnap. All rights reserved.Legal|Privacy policy|Modern Slavery Act Transparency Statement|Sitemap|About US| Contact US: help@patsnap.com