Model Calibration System and Method Based on Wing Tip Braking Device of High-Lift Control System
A control system and wingtip technology, applied in the field of aviation testing, can solve the problems of large model calibration workload, reduced model simulation confidence of flap and slat wingtip brakes, uncontrollable process, etc., to shorten the research and development cycle and cost, The effect of reducing the number of physical verifications and reducing the test conditions
- Summary
- Abstract
- Description
- Claims
- Application Information
AI Technical Summary
Problems solved by technology
Method used
Image
Examples
Embodiment 1
[0033] Step 1: Input the influencing factors and levels (influencing factors such as: voltage; levels such as: 18vDC, 20Vdc, 24Vdc) on the wingtip brake object 2 to the experimental design module 1, and use the experimental design method to generate a variety of test conditions and corresponding The sequence of working conditions, the test working conditions include parameters corresponding to the wingtip brake object 2, the wingtip brake controller 3, the hardware-in-the-loop simulator 4, and the variable load object 8;
[0034] Step 2: The experimental design module 1 inputs the initial value of parameters (such as the moment of inertia of the variable load object 8) to the variable load object 8 according to the test condition 1, and inputs the target speed and Torque; the variable load object 8 operates according to the initial value of the input parameters, and at the same time, the variable load object 8 feeds back the torque and speed information to the hardware-in-the-l...
PUM
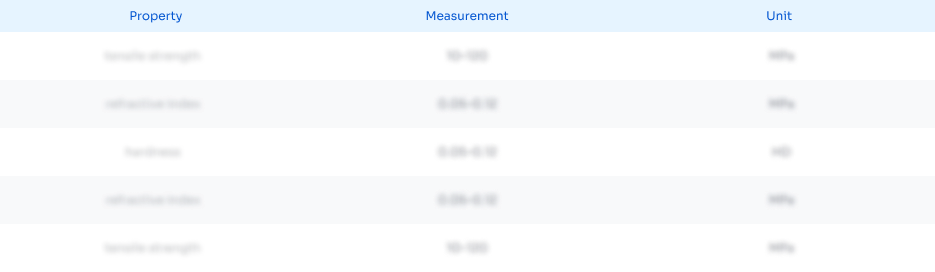
Abstract
Description
Claims
Application Information

- R&D
- Intellectual Property
- Life Sciences
- Materials
- Tech Scout
- Unparalleled Data Quality
- Higher Quality Content
- 60% Fewer Hallucinations
Browse by: Latest US Patents, China's latest patents, Technical Efficacy Thesaurus, Application Domain, Technology Topic, Popular Technical Reports.
© 2025 PatSnap. All rights reserved.Legal|Privacy policy|Modern Slavery Act Transparency Statement|Sitemap|About US| Contact US: help@patsnap.com