Polyurethane resin for waterproof vapor permeable leather and preparation method of polyurethane resin
A technology for polyurethane resin and leather, applied in the field of polyurethane resin, can solve the problems of no waterproof effect, decreased vapor permeability, etc., and achieve the effects of simple and easy operation, excellent velvet feeling, and avoiding the existence of large pores
- Summary
- Abstract
- Description
- Claims
- Application Information
AI Technical Summary
Problems solved by technology
Method used
Image
Examples
Embodiment 1
[0025] (1) Polybutylene adipate diol (0.05mol), polytetrahydrofuran ether diol (0.05mol), double-terminal hydroxyl long-chain alkyl silicone oil (0.01mol), solvent N,N-dimethyl Mix formamide (100ml), add 4,4'-diphenylmethane diisocyanate (0.088mol), and react at 75°C until the content of isocyanate groups is constant;
[0026] (2) Add ethylene glycol (0.23mol), N,N-dimethylformamide (80ml), add 4,4'-diphenylmethane diisocyanate (0.224mol), react at 75°C for 1 hour, add solvent Add 4,4'-diphenylmethane diisocyanate (0.032mol) to N,N-dimethylformamide (194ml), and stop adding when the viscosity reaches 120Pa·s (25°C). Methanol (0.003mol) was added to stop the reaction, and after 30 minutes, the temperature was lowered to 50°C and the material was discharged to obtain the polyurethane resin with a solid mass fraction of 30%.
Embodiment 2
[0028] (1) Polyhexamethylene adipate diol (0.08mol), polypropylene glycol (0.02mol), double-ended hydroxyl long-chain alkyl silicone oil (0.003mol), double-ended hydroxyl polytrifluoropropylmethylsilane Put oxane (0.002mol) and solvent N,N-dimethylformamide (100ml) into the reaction flask, mix well, put in 4,4'-diphenylmethane diisocyanate (0.08mol), react at 75°C until Constant isocyanate group content;
[0029] (2) After the prepolymerization is completed, add ethylene glycol (0.316mol), solvent N,N-dimethylformamide (80ml), add 4,4'-diphenylmethane diisocyanate (0.32mol), 75°C React for 1 hour, add the remaining solvent N,N-dimethylformamide (210g), continue to add 4,4'-diphenylmethane diisocyanate (0.02mol), the viscosity rises to 100Pa·s (25°C ) viscosity, stop adding. Methanol (0.003mol) was added to stop the reaction, and after 30 minutes, the temperature was lowered to 50°C and the material was discharged to obtain the polyurethane resin with a solid mass fraction of...
Embodiment 3
[0031] (1) Polybutylene adipate diol (0.04mol), polytetrahydrofuran ether diol (0.06mol), double-ended hydroxyl long-chain alkyl silicone oil (0.006mol), double-ended hydroxyl polytrifluoropropyl Add methylsiloxane (0.002mol) and solvent N,N-dimethylformamide (100ml) into the reaction flask, mix well, add 4,4'-diphenylmethane diisocyanate (0.339mol), and heat at 75°C Reaction until the isocyanate group content is constant;
[0032] (2) After the prepolymerization is completed, add ethylene glycol (0.271mol), solvent N,N-dimethylformamide (80ml), add 4,4'-diphenylmethane diisocyanate (0.272mol), 75°C React for 1 hour, add the remaining solvent N,N-dimethylformamide (200g), continue to add 4,4'-diphenylmethane diisocyanate (0.016mol), the viscosity rises to 80Pa·s (25°C) When viscosity is reached, stop adding. Methanol (0.003mol) was added to stop the reaction, and after 30 minutes, the temperature was lowered to 50°C and the material was discharged to obtain the polyurethane ...
PUM
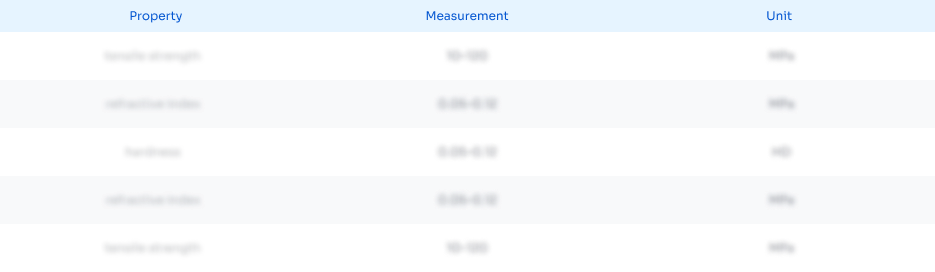
Abstract
Description
Claims
Application Information

- R&D Engineer
- R&D Manager
- IP Professional
- Industry Leading Data Capabilities
- Powerful AI technology
- Patent DNA Extraction
Browse by: Latest US Patents, China's latest patents, Technical Efficacy Thesaurus, Application Domain, Technology Topic, Popular Technical Reports.
© 2024 PatSnap. All rights reserved.Legal|Privacy policy|Modern Slavery Act Transparency Statement|Sitemap|About US| Contact US: help@patsnap.com