Ultra-large solid rocket engine sectional composite shell and manufacture method thereof
A technology of solid rockets and composite materials, which is applied to the field of segmented composite material shells of super-large solid rocket motors and its manufacturing field, can solve the problems of high cost, high propellant price, and propellant cannot be poured at one time, and reduces the The effect of waste, simple and efficient assembly, and transportation cost saving
- Summary
- Abstract
- Description
- Claims
- Application Information
AI Technical Summary
Problems solved by technology
Method used
Image
Examples
Embodiment 1
[0056] see Figure 1-2As shown, Embodiment 1 of the present invention provides a segmented composite shell of an ultra-large solid rocket motor, which includes a shell body 1, and openings 10 are provided at both ends of the shell body 1, and the shell body 1 is composed of a plurality of The prefabricated parts are assembled, and the multiple prefabricated parts include the middle section 11 and the front head section 12 and the rear head section 13 connected to the two ends of the middle section 11 respectively, the middle section 11, the front head section 12 and the rear head section 13 It can be manufactured at the launch site or manufactured in sections at the factory and then transported to the launch site. Two openings 10 are respectively set on the front head section 12 and the rear head section 13. The shell body 1 is a cavity connected at both ends, which is convenient for manufacturing. During the solid rocket motor, the propellant is poured in the cavity; the end ...
Embodiment 2
[0061] Embodiment 2 of the present invention provides a method for manufacturing a solid rocket motor using a super-large solid rocket motor segmented composite shell, see Figure 1-2 As shown, the super-large solid rocket motor segmented composite material casing provided includes a casing body 1, and openings 10 are opened at both ends of the casing body 1, and the casing body 1 is assembled from a plurality of prefabricated parts. A prefabricated part comprises a middle section 11 and a front head section 12 and a rear head section 13 which are respectively connected to the two ends of the middle section 11. The middle section 11, the front head section 12 and the back head section 13 can be manufactured at the launch site or in a factory. Manufactured in sections and then transported to the launch site, two openings 10 are respectively arranged in the front head section 12 and the rear head section 13, and the inside of the shell body 1 is a cavity connected at both ends, w...
Embodiment 3
[0077] A method for manufacturing a solid rocket motor using a segmented composite shell of an ultra-large solid rocket motor comprises the following steps:
[0078] S1. Wrap the outer surface of the front head section 12 along the hoop direction for the first time to form the first winding layer 16, and wrap the middle section 11 on its outer surface along the hoop direction for the first time to form the first winding layer. 16. The rear head section 13 is wrapped around its outer surface for the first time in the circumferential direction to form the first winding layer 16;
[0079] S2. After the first wrapping layer 16 of the front head section 12, the middle section 11 and the rear head section 13 is solidified, pour propellant into the front head section 12, the middle section 11 and the back head section 13 respectively, After the propellant is solidified, the grain column in the front head section 12 has a through cavity extending along its axial direction, the grain c...
PUM
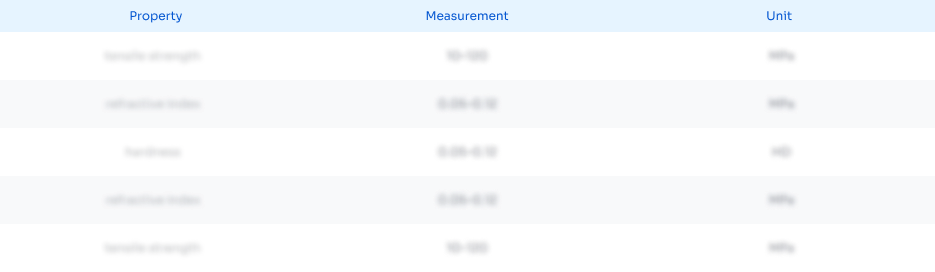
Abstract
Description
Claims
Application Information

- R&D
- Intellectual Property
- Life Sciences
- Materials
- Tech Scout
- Unparalleled Data Quality
- Higher Quality Content
- 60% Fewer Hallucinations
Browse by: Latest US Patents, China's latest patents, Technical Efficacy Thesaurus, Application Domain, Technology Topic, Popular Technical Reports.
© 2025 PatSnap. All rights reserved.Legal|Privacy policy|Modern Slavery Act Transparency Statement|Sitemap|About US| Contact US: help@patsnap.com