Method for preparing high-purity hafnium by calcium in-situ distillation-deoxidation
A high-purity, in-situ technology, applied in the field of metal smelting, can solve the problems of high energy consumption and pollution of hafnium products, and achieve the effects of reducing energy consumption, high solubility, and reducing activity
- Summary
- Abstract
- Description
- Claims
- Application Information
AI Technical Summary
Benefits of technology
Problems solved by technology
Method used
Image
Examples
Embodiment 1
[0035] Take 1 metal hafnium block, the mass is 20g, the oxygen content is 850ppm, press (CaCl 2): m(Hf)=5:1 Weigh 100g of anhydrous calcium chloride (dehydrated at 300°C for 24 hours before use), and weigh 4g of high-purity calcium chips (at 900°C, calcium in anhydrous calcium chloride molten salt 0.5 times the saturation solubility), metal hafnium and anhydrous calcium chloride are filled in the hafnium crucible, high-purity calcium chips are filled in the gap between the hafnium crucible and the stainless steel crucible, and then the stainless steel crucible is sealed with a high-temperature sealing gasket. Specific as attached figure 1 shown.
[0036] Put the sealed crucible into a vacuum tank heated by a resistance furnace, cover the furnace cover, vacuumize to 0.5 Pa, and then wash with argon. Under argon protection, heat up to 900°C at 5°C / min, and keep at 900°C for 40 hours. After the heat preservation is over, the furnace is cooled to room temperature. After coming ...
Embodiment 2
[0038] Take 1 metal hafnium block, with a mass of 20g and an oxygen content of 760ppm, press (CaCl 2 ): m(Hf)=20:1 Weigh 400g of anhydrous calcium chloride (dehydrated at 300°C for 36h before use), weigh 57g of industrial calcium chips (at 1050°C, calcium saturated in anhydrous calcium chloride molten salt 2 times the solubility), metal hafnium and anhydrous calcium chloride are filled in the hafnium crucible, industrial calcium chips are filled in the gap between the hafnium crucible and the stainless steel crucible, and then the stainless steel crucible is sealed with a high-temperature sealing gasket, specifically as follows attached figure 1 shown.
[0039] Put the sealed crucible into a vacuum tank heated by a resistance furnace, cover the furnace cover, vacuumize to 0.1Pa, and then wash with argon. Under argon protection, heat up to 1050°C at 5°C / min, and keep at 1050°C for 20 hours. After the heat preservation is over, the furnace is cooled to room temperature. After...
Embodiment 3
[0041] Get 1 metal hafnium wire, quality 15g, oxygen content 910ppm, press (CaCl 2 ): m(Hf)=40:1 Weigh 600g of anhydrous calcium chloride (dehydrated at 400°C for 19h before use), weigh 213g of industrial calcium chips (at 1100°C, calcium saturated in anhydrous calcium chloride molten salt 4 times of the solubility), metal hafnium and anhydrous calcium chloride are filled in the hafnium crucible, industrial calcium chips are filled in the gap between the hafnium crucible and the stainless steel crucible, and then the stainless steel crucible is sealed with a high-temperature sealing gasket, specifically as follows attached figure 1 shown.
[0042] Put the sealed crucible into a vacuum tank heated by a resistance furnace, cover the furnace cover, vacuumize to 0.2Pa, and then wash with argon. Under the protection of argon, heat up to 1100°C at 5°C / min, and keep at 1100°C for 14 hours. After the heat preservation is over, the furnace is cooled to room temperature. After coming...
PUM
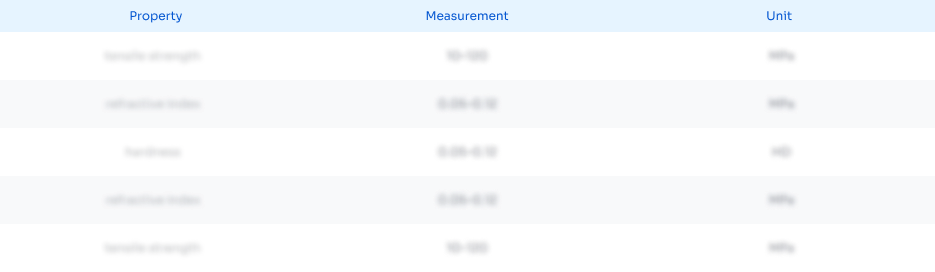
Abstract
Description
Claims
Application Information

- R&D
- Intellectual Property
- Life Sciences
- Materials
- Tech Scout
- Unparalleled Data Quality
- Higher Quality Content
- 60% Fewer Hallucinations
Browse by: Latest US Patents, China's latest patents, Technical Efficacy Thesaurus, Application Domain, Technology Topic, Popular Technical Reports.
© 2025 PatSnap. All rights reserved.Legal|Privacy policy|Modern Slavery Act Transparency Statement|Sitemap|About US| Contact US: help@patsnap.com