Intelligent wing composite-material trailing edge system
A composite material, trailing edge technology, used in wing adjustment and other directions to reduce noise and improve aerodynamic efficiency
- Summary
- Abstract
- Description
- Claims
- Application Information
AI Technical Summary
Problems solved by technology
Method used
Image
Examples
Embodiment Construction
[0019] The present invention will be described in detail below in conjunction with the drawings:
[0020] 1 General layout of the trailing edge of the intelligent wing composite material
[0021] The overall layout of the trailing edge of the intelligent wing composite material is that the trailing edge is located at the rear of the wing and is seamlessly connected to the wing stabilizer 19; the trailing edge structure is a full-height honeycomb structure with a base plate; the driver is located in the stabilizer 19, made of steel The cable 6 is connected to the end of the trailing edge, and each limit post 7 controls the position of the steel cable 6 and cooperates with the control computer 15 to drive the trailing edge; the fiber grating is located in the composite substrate 3 to realize the deformation perception of the trailing edge.
[0022] 2 trailing edge structure
[0023] The rear edge structure is composed of a large deformation skin 1, a flexible honeycomb 2, a composite ma...
PUM
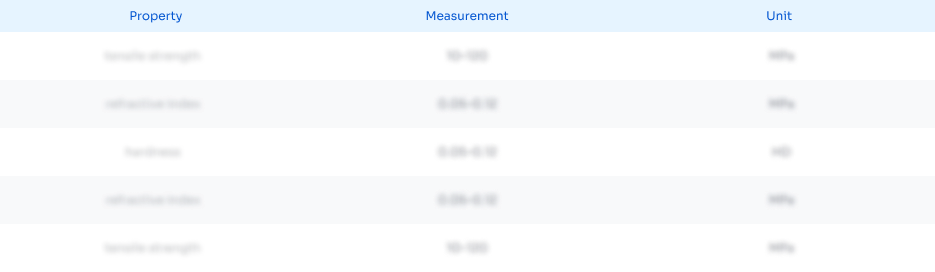
Abstract
Description
Claims
Application Information

- Generate Ideas
- Intellectual Property
- Life Sciences
- Materials
- Tech Scout
- Unparalleled Data Quality
- Higher Quality Content
- 60% Fewer Hallucinations
Browse by: Latest US Patents, China's latest patents, Technical Efficacy Thesaurus, Application Domain, Technology Topic, Popular Technical Reports.
© 2025 PatSnap. All rights reserved.Legal|Privacy policy|Modern Slavery Act Transparency Statement|Sitemap|About US| Contact US: help@patsnap.com