Precise control method of rudder speed and position for electromechanical hydrostatic servo system
A servo system and precise control technology, applied in the direction of motor generator control, control of electromechanical brakes, AC motor control, etc., can solve the problems of single control variable and high noise, achieve effective protection mechanism, eliminate startup noise, and reduce vibration. Effect
- Summary
- Abstract
- Description
- Claims
- Application Information
AI Technical Summary
Problems solved by technology
Method used
Image
Examples
Embodiment
[0024] The stroke of the servo mechanism used in a certain project is ±300mm, the required maximum rudder speed is ±30mm / s, the position accuracy is ±1mm, the controllable average speed accuracy is ±3mm / s, the motor speed is 0~±1800rpm, the position (rudder Angle) mode, when the set position is a specific position, the position sensor connected to the actuator will detect the position of the steering gear in real time, and calculate the average steering speed according to the 100ms cycle. When the average speed of the steering gear deviates from the maximum steering speed , adjust the extreme value of the motor speed limit, so that the current rudder speed follows the maximum rudder speed, and its absolute value is maintained within the range of 30mm / s. Inertia, the average rudder speed measured at this time is relatively low, and the rudder speed at this time is set at a speed of 20mm / s to prevent the motor speed from being too high and the mechanism to vibrate to ensure a smo...
PUM
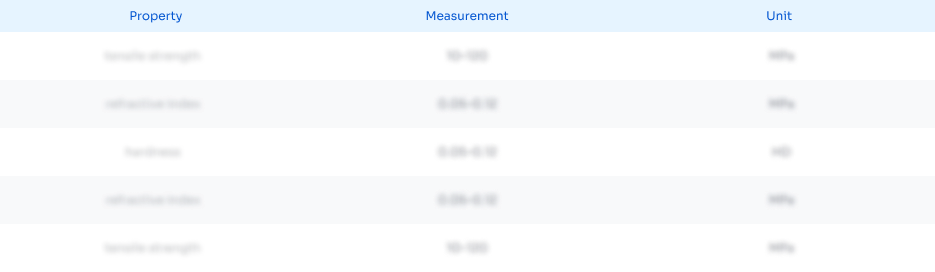
Abstract
Description
Claims
Application Information

- Generate Ideas
- Intellectual Property
- Life Sciences
- Materials
- Tech Scout
- Unparalleled Data Quality
- Higher Quality Content
- 60% Fewer Hallucinations
Browse by: Latest US Patents, China's latest patents, Technical Efficacy Thesaurus, Application Domain, Technology Topic, Popular Technical Reports.
© 2025 PatSnap. All rights reserved.Legal|Privacy policy|Modern Slavery Act Transparency Statement|Sitemap|About US| Contact US: help@patsnap.com