Monorail crane self-balancing compensation heavy hydraulic lifting beam
A technology of self-balancing and lifting beams, which is applied in the direction of track system, load hanging components, safety devices, etc., can solve the problems that the carrying capacity is not as good as the surface contact, cannot transport the hydraulic support, and the safety is not guaranteed, so as to increase the carrying capacity, The effect of smooth and safe transportation, guarantee of life and property safety
- Summary
- Abstract
- Description
- Claims
- Application Information
AI Technical Summary
Problems solved by technology
Method used
Image
Examples
Embodiment Construction
[0027] The following will clearly and completely describe the technical solutions in the embodiments of the present invention with reference to the accompanying drawings in the embodiments of the present invention. Obviously, the described embodiments are only some, not all, embodiments of the present invention. Based on the embodiments of the present invention, all other embodiments obtained by persons of ordinary skill in the art without making creative efforts belong to the protection scope of the present invention.
[0028] like Figure 4 to Figure 5 , the present invention proposes a monorail crane self-balancing compensation heavy-duty hydraulic lifting beam, which includes: an arched beam 1, a beam 2, a longitudinal beam 3, and a connecting pin 5 between the beam and the longitudinal beam as the main body of the lifting beam;
[0029] Described arched crossbeam 1 comprises crossbeam main body 1-1, walking trolley fixed beam 1-2 and walking trolley 1-3; Crossbeam main bo...
PUM
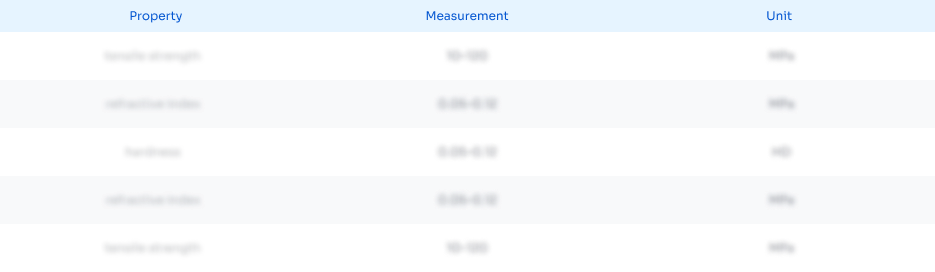
Abstract
Description
Claims
Application Information

- R&D
- Intellectual Property
- Life Sciences
- Materials
- Tech Scout
- Unparalleled Data Quality
- Higher Quality Content
- 60% Fewer Hallucinations
Browse by: Latest US Patents, China's latest patents, Technical Efficacy Thesaurus, Application Domain, Technology Topic, Popular Technical Reports.
© 2025 PatSnap. All rights reserved.Legal|Privacy policy|Modern Slavery Act Transparency Statement|Sitemap|About US| Contact US: help@patsnap.com