Whole-cabin vibration absorbing device without resonance peak
A vibration reduction device and resonance peak technology, which is applied in transportation and packaging, non-rotational vibration suppression, space navigation equipment, etc., can solve the problems of random frequency and magnitude, unfavorable flight safety, corresponding displacement value and large stress, etc. problem, to achieve the effect of increasing thermal resistance, improving comfort, and meeting temperature control requirements
- Summary
- Abstract
- Description
- Claims
- Application Information
AI Technical Summary
Problems solved by technology
Method used
Image
Examples
Embodiment Construction
[0020] The present invention will be described in further detail below in conjunction with the accompanying drawings.
[0021] The whole cabin vibration reduction scheme without resonance peak includes:
[0022] a) Cancel the single-machine shock absorber, and connect multiple zero-stiffness vibration isolators or shock absorbers without resonance peaks in series between the cabin section to be damped and the cabin support;
[0023] b) Application of structural damping heat pipe integrated deck, such as installing heat pipes in metal honeycomb sandwich panels to achieve isothermalization, filling metal particles in honeycomb sandwich cores for vibration reduction, etc.;
[0024] c) According to the size, weight, heat consumption, etc. of the cabin to be damped, different vibration damping schemes are combined.
[0025] The whole cabin vibration reduction design process without resonance peak:
[0026] a) First sort out the constraints of the cabin to be damped, such as vibra...
PUM
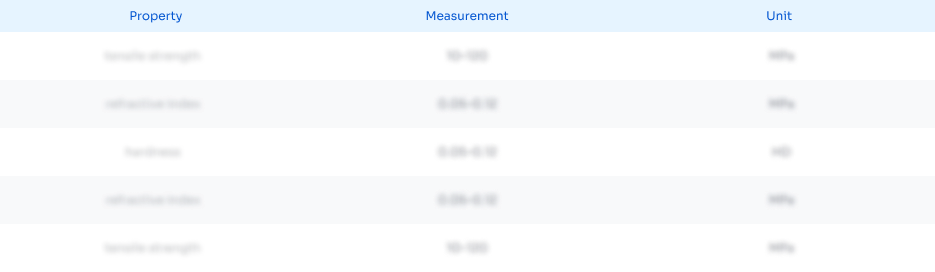
Abstract
Description
Claims
Application Information

- R&D
- Intellectual Property
- Life Sciences
- Materials
- Tech Scout
- Unparalleled Data Quality
- Higher Quality Content
- 60% Fewer Hallucinations
Browse by: Latest US Patents, China's latest patents, Technical Efficacy Thesaurus, Application Domain, Technology Topic, Popular Technical Reports.
© 2025 PatSnap. All rights reserved.Legal|Privacy policy|Modern Slavery Act Transparency Statement|Sitemap|About US| Contact US: help@patsnap.com