Industrial robot digital twin real-time job control, monitoring and precision compensation method
An industrial robot and real-time operation technology, which is applied in the direction of program-controlled manipulators, manipulators, manufacturing tools, etc., can solve the problems of failure to combine digital twins, information islands, and few application explorations of industrial robot digital twins, so as to improve operating efficiency The effect of interaction with flexibility and production information
- Summary
- Abstract
- Description
- Claims
- Application Information
AI Technical Summary
Problems solved by technology
Method used
Image
Examples
Embodiment Construction
[0014] combine figure 1 , a method for real-time operation control, monitoring and precision compensation of an industrial robot digital twin, characterized in that it includes the following steps:
[0015] S101, constructing the digital twin model of the robot and the model of the workpiece in the digital twin modeling software, ensuring the relative position accuracy of the two through three-point positioning, and generating robot operation instructions through model simulation based on the processing technology;
[0016] S102, the data communication service program simultaneously establishes a connection with the simulation software and the robot controller through the manufacturer's open interface, converts the operation instruction into a robot standard control instruction to control the robot operation, and stores the twin data;
[0017] S103, the data communication service program collects the real-time robot joint angle through the external high-precision measuring ins...
PUM
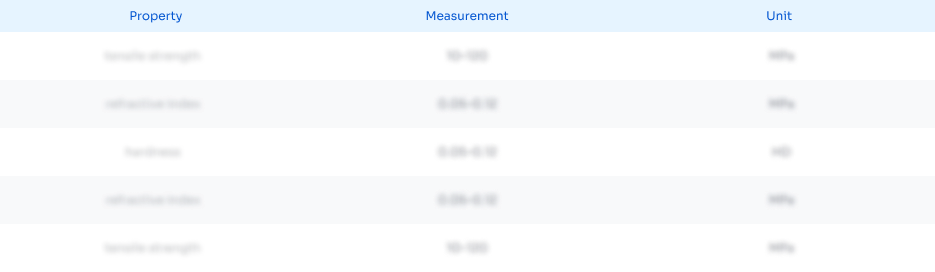
Abstract
Description
Claims
Application Information

- R&D Engineer
- R&D Manager
- IP Professional
- Industry Leading Data Capabilities
- Powerful AI technology
- Patent DNA Extraction
Browse by: Latest US Patents, China's latest patents, Technical Efficacy Thesaurus, Application Domain, Technology Topic, Popular Technical Reports.
© 2024 PatSnap. All rights reserved.Legal|Privacy policy|Modern Slavery Act Transparency Statement|Sitemap|About US| Contact US: help@patsnap.com